Low-density ablation-resistant ethylene propylene diene monomer material and preparation method thereof
A technology of EPDM rubber and reinforcing filler is applied in the field of heat-resistant materials, which can solve the problems of affecting the loading coefficient, increasing the negative mass of the rocket engine, and burning through the thermal insulation layer.
- Summary
- Abstract
- Description
- Claims
- Application Information
AI Technical Summary
Problems solved by technology
Method used
Image
Examples
Embodiment 1
[0047] 1) Add 100 parts of EPDM rubber, 25 parts of reinforcing filler, 15 parts of organic fiber, 5 parts of inorganic fiber, 5 parts of ammonium salt flame retardant, 3 parts of lightweight filler, 10 parts of metal hydroxide filler, 20 parts of tackifying resin and 5 parts of petroleum-based softener are added to the internal mixer and mixed evenly, and the highest mixing temperature does not exceed 90°C;
[0048] 2) Add 2 parts of peroxide vulcanizing agent to 1) the internal mixer and mix evenly, and the maximum mixing temperature shall not exceed 60°C;
[0049] 3) The product obtained in 2) is then thinned and passed uniformly in an open mill, and the sheet is produced;
[0050] 4) The product obtained in 3) is vulcanized in a flat vulcanizing machine at 10Mpa and 160°C for 50 minutes.
Embodiment 2
[0052] 1) Add 100 parts of EPDM rubber, 20 parts of reinforcing filler, 10 parts of organic fiber, 10 parts of inorganic fiber, 5 parts of ammonium salt flame retardant, 5 parts of lightweight filler, 10 parts of metal hydroxide filler, 20 parts of tackifying resin and 5 parts of petroleum-based softener are added to the internal mixer and mixed evenly, and the highest mixing temperature does not exceed 90°C;
[0053] 2) Then add 3 parts of peroxide vulcanizing agent to 1) internal mixer and mix evenly, the maximum mixing temperature shall not exceed 60°C;
[0054] 3) The product obtained in 2) is then thinned and passed uniformly in an open mill, and the sheet is produced;
[0055] 4) The product obtained in 3) is vulcanized in a flat vulcanizing machine at 10Mpa and 160°C for 50 minutes.
Embodiment 3
[0057] 1) Add 100 parts of EPDM rubber, 20 parts of reinforcing filler, 10 parts of organic fiber, 10 parts of inorganic fiber, 10 parts of ammonium salt flame retardant, 3 parts of lightweight filler, 5 parts of metal hydroxide filler, 20 parts of tackifying resin and 5 parts of petroleum-based softener are added to the internal mixer and mixed evenly, and the highest mixing temperature does not exceed 90°C;
[0058] 2) Add 2 parts of peroxide vulcanizing agent to 1) the internal mixer and mix evenly, and the maximum mixing temperature shall not exceed 60°C;
[0059] 3) The product obtained in 2) is then thinned and passed uniformly in an open mill, and the sheet is produced;
[0060] 4) The product obtained in 3) is vulcanized in a flat vulcanizing machine at 10Mpa and 160°C for 50 minutes.
PUM
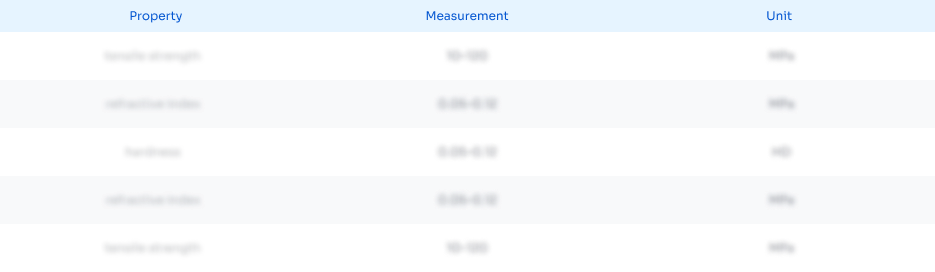
Abstract
Description
Claims
Application Information

- R&D Engineer
- R&D Manager
- IP Professional
- Industry Leading Data Capabilities
- Powerful AI technology
- Patent DNA Extraction
Browse by: Latest US Patents, China's latest patents, Technical Efficacy Thesaurus, Application Domain, Technology Topic, Popular Technical Reports.
© 2024 PatSnap. All rights reserved.Legal|Privacy policy|Modern Slavery Act Transparency Statement|Sitemap|About US| Contact US: help@patsnap.com