Insulation board forming process based on environment-friendly foaming process and processing system of insulation board forming process
A molding process and processing system technology, applied in the field of insulation board molding process and its processing system, to achieve the effect of ensuring environmental protection performance
- Summary
- Abstract
- Description
- Claims
- Application Information
AI Technical Summary
Problems solved by technology
Method used
Image
Examples
Embodiment 1
[0039] refer to figure 1 , the insulation board molding process based on the environmentally friendly foaming process, including the following process steps,
[0040] S1. Raw materials are mixed, flame retardant is added in the recycled material, and the recycled material is made into recycled material with the same particle size through the crusher 2, 1 kg of flame retardant and 5-9 kg of recycled material; Put the fuel mixture into a 2t mixing tank and stir for 8 hours to make a mixture;
[0041] S2. Sampling inspection of raw materials. After the mixing is completed, the mixture is sampled and tested. After the sampled mixture is finished by a small extruder, the oxygen index and melt index of the finished product are tested;
[0042] S3. Secondary stirring, add adhesive to the mixture in the mixer, the adhesive is set as adhesive oil, wherein 300 kg of mixed material is added with 2-3 kg of adhesive oil, the adhesive oil can be aviation oil or Edible oil. At present, in ...
Embodiment 2
[0051] refer to figure 2 and image 3 , a processing system for forming insulation boards based on environmentally friendly foaming technology, including a melting system 1, a crusher 2, and a screening system 3. The scraps of the insulation board pass through the melting system 1, the crusher 2, and the screening system 3 in turn to make recycled materials.
[0052] refer to figure 2 and image 3 , the melting system 1 includes a melting extruder 26 and a die head 4 fixedly connected to the discharge port of the melting extruder 26, the die head 4 is provided with a plurality of die holes 5 for extruding strips, and the melted The edge material is extruded into strips, in order to facilitate the cooling of the strips, a conveying frame 6 is arranged between the melt extruder 26 and the crusher 2, and the conveying frame 6 is placed on the ground, and the transmission frame 6 is connected effectively On the conveyor belt 7 for feeding, the conveyor frame 6 is rotatably co...
PUM
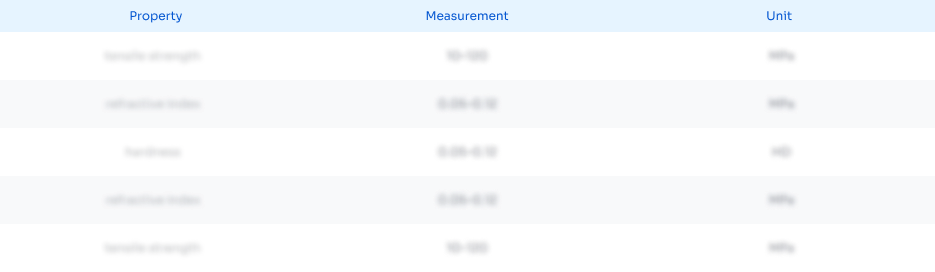
Abstract
Description
Claims
Application Information

- R&D
- Intellectual Property
- Life Sciences
- Materials
- Tech Scout
- Unparalleled Data Quality
- Higher Quality Content
- 60% Fewer Hallucinations
Browse by: Latest US Patents, China's latest patents, Technical Efficacy Thesaurus, Application Domain, Technology Topic, Popular Technical Reports.
© 2025 PatSnap. All rights reserved.Legal|Privacy policy|Modern Slavery Act Transparency Statement|Sitemap|About US| Contact US: help@patsnap.com