Uniaxial weft-knitted fabric and manufacturing method
A weft-knitted fabric and uniaxial technology, which is applied in weft-knitting, textiles, papermaking, knitting, etc., can solve the problems of limiting the elasticity of warp-knitted uniaxial fabrics and failing to meet the performance requirements of petroleum expansion pipe materials.
- Summary
- Abstract
- Description
- Claims
- Application Information
AI Technical Summary
Problems solved by technology
Method used
Image
Examples
Embodiment 1
[0019] Embodiment 1: As a kind of example of specific implementation, provide a kind of uniaxial weft knitting fabric, comprise: as the high-strength polyester weft flat knitting structure of binding system, as the T300 carbon fiber lining warp yarn system that improves warp direction high strength, its It is characterized in that the lining warp yarns are interlaced between the sinker arcs of the weft plain stitches in a parallel and straight manner, and the weft plain stitches are looped by knitting needles, and then formed by threading the loops. Preferably, the yarn used in the binding system is 75D×2 high-strength polyester. Preferably, the yarn used in the lining warp yarn system is T300-12K carbon fiber. The preparation method of described uniaxial weft knitted fabric is as follows:
[0020] (1) Needle row: Select a flat knitting machine with a machine number of 6G, design the number of needles to be 60, and push it to the working position to ensure that the knitting n...
Embodiment 2
[0024] Embodiment 2: As an example of a specific embodiment, a kind of uniaxial weft knitted fabric is provided, including: a weft plain stitch as a binding system, as a carbon fiber and glass fiber hybrid interlining system that improves high strength in the warp direction, It is characterized in that the lining warp yarns are interlaced between the sinker arcs of the weft plain stitches in a parallel and straight manner, and the weft plain stitches are looped by knitting needles, and then formed by threading the loops. Preferably, the yarn used in the binding system is 48-count aramid spun yarn. Preferably, the yarns used in the lining warp yarn system are T300-6K carbon fiber and 1560dtex glass fiber. The preparation method of described uniaxial weft knitted fabric is as follows:
[0025] (1) Needle row: Select a flat knitting machine with a machine number of 6G, design the number of needles to be 60, and push it to the working position to ensure that the knitting needles ...
PUM
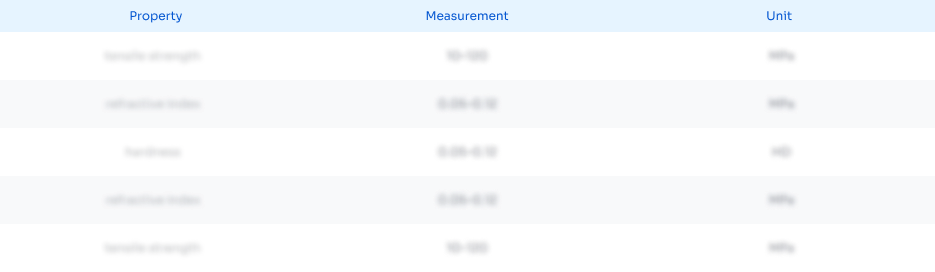
Abstract
Description
Claims
Application Information

- R&D
- Intellectual Property
- Life Sciences
- Materials
- Tech Scout
- Unparalleled Data Quality
- Higher Quality Content
- 60% Fewer Hallucinations
Browse by: Latest US Patents, China's latest patents, Technical Efficacy Thesaurus, Application Domain, Technology Topic, Popular Technical Reports.
© 2025 PatSnap. All rights reserved.Legal|Privacy policy|Modern Slavery Act Transparency Statement|Sitemap|About US| Contact US: help@patsnap.com