Solid waste pyrolysis and oil gas catalytic reforming system
A catalytic reforming and solid waste technology, applied in incinerators, hydrocarbon oil treatment, petroleum industry, etc., can solve the problems of easy condensation of pyrolysis oil, blockage of pipelines, unstable operation of pyrolysis system, etc.
- Summary
- Abstract
- Description
- Claims
- Application Information
AI Technical Summary
Problems solved by technology
Method used
Image
Examples
Embodiment 1
[0066] use figure 1 The shown solid waste pyrolysis and oil-gas catalytic reforming system processes agricultural straw as follows:
[0067] Agricultural straw enters the pyrolysis chamber 6 from the feed port 8, and undergoes a pyrolysis reaction at 550°C to obtain pyrolysis oil gas and pyrolysis charcoal. The components of the pyrolysis oil are high-temperature pyrolysis oil, CH 4 、H 2 , CO, CO 2 and small amounts of hydrocarbon gases;
[0068] The pyrolysis oil gas enters the catalytic reforming reactor 2 from the oil gas inlet 13, and H is added from the gasification agent inlet 14 2 O and O 2 Gasification agent, H 2 O and O 2 The amount of gasification agent introduced is 25% and 30% of the mass of oil and gas respectively, and the catalytic reforming reaction is carried out at 800°C to obtain the composition of CH 4 、H 2 , CO, CO 2 The mixed gas, the resulting gas is discharged from the gas outlet 15; wherein the catalyst in the catalytic reforming reactor 2 is ...
Embodiment 2
[0074] use figure 1 The shown solid waste pyrolysis and oil-gas catalytic reforming system processes plastic waste in the following ways:
[0075] Plastic waste enters the pyrolysis chamber 6 from the feed port 8, and undergoes a pyrolysis reaction at 500°C to obtain pyrolysis oil gas and pyrolysis charcoal, wherein the components of the pyrolysis oil are high-temperature pyrolysis oil, CH 4 、H 2 , CO, CO 2 and small amounts of hydrocarbon gases;
[0076] The pyrolysis oil gas enters the catalytic reforming reactor 2 from the oil gas inlet 13, and H is added from the gasification agent inlet 14 2 O and O 2 Gasification agent, H 2 O and O 2 The amount of gasification agent introduced is 35% and 35% of the mass of oil and gas respectively, and the catalytic reforming reaction is carried out at 850°C, and the composition is CH 4 、H 2 , CO, CO 2 The gas, the gas obtained is discharged from the gas outlet 15; wherein the catalyst in the catalytic reforming reactor 2 is an ...
PUM
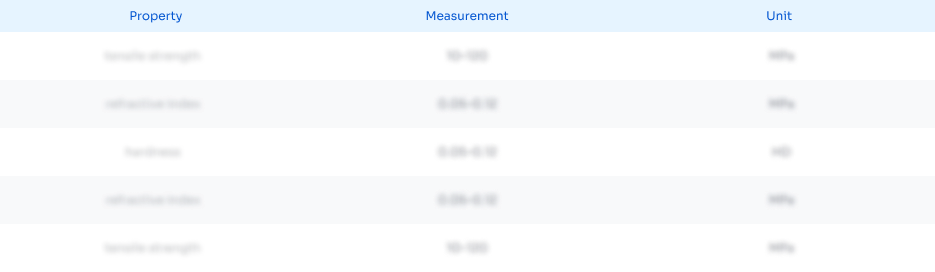
Abstract
Description
Claims
Application Information

- R&D
- Intellectual Property
- Life Sciences
- Materials
- Tech Scout
- Unparalleled Data Quality
- Higher Quality Content
- 60% Fewer Hallucinations
Browse by: Latest US Patents, China's latest patents, Technical Efficacy Thesaurus, Application Domain, Technology Topic, Popular Technical Reports.
© 2025 PatSnap. All rights reserved.Legal|Privacy policy|Modern Slavery Act Transparency Statement|Sitemap|About US| Contact US: help@patsnap.com