Automatic calibrating device for standard metal measuring vessel
A standard metal gauge, automatic verification technology, applied in measuring devices, testing/calibrating devices, testing/calibrating volume flow, etc., can solve problems such as increased uncertainty, low efficiency, and easy water storage at the bottom valve position.
- Summary
- Abstract
- Description
- Claims
- Application Information
AI Technical Summary
Problems solved by technology
Method used
Image
Examples
Embodiment Construction
[0034] Such as Figure 1-9 As shown, the present invention includes an upper cone, a cylindrical body and a lower cone connected to each other. It is characterized in that the upper end of the upper cone is connected with a metering neck and a liquid level tube, and the liquid level tube is provided with a metering neck scale. The control valve on the neck is connected with a three-way valve at the lower end of the lower cone.
[0035] The end of the spool of the three-way valve far away from the valve port is fixedly connected with a gear. The gear is connected to a screw meshing transmission. The screw is fixed on the outer wall of the three-way valve through the mounting frame, and the screw can rotate relative to the mounting frame. Driven by a stepping motor; the stepping motor acts to drive the screw connected to it to rotate, the screw is meshed with the gear for transmission, and the gear rotates accordingly, driving the valve core to rotate.
[0036] The control valv...
PUM
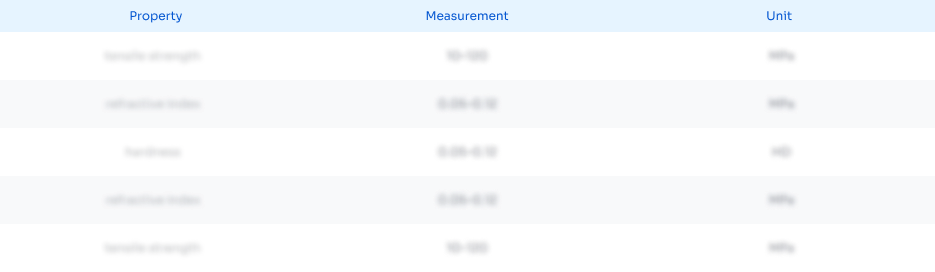
Abstract
Description
Claims
Application Information

- R&D
- Intellectual Property
- Life Sciences
- Materials
- Tech Scout
- Unparalleled Data Quality
- Higher Quality Content
- 60% Fewer Hallucinations
Browse by: Latest US Patents, China's latest patents, Technical Efficacy Thesaurus, Application Domain, Technology Topic, Popular Technical Reports.
© 2025 PatSnap. All rights reserved.Legal|Privacy policy|Modern Slavery Act Transparency Statement|Sitemap|About US| Contact US: help@patsnap.com