Method for dehydrogenating hydrogen-containing substance
A dehydrogenation and material technology, applied in chemical instruments and methods, hydrogen, metal/metal oxide/metal hydroxide catalysts, etc., can solve problems such as cracking, catalyst activity reduction, deactivation, etc.
- Summary
- Abstract
- Description
- Claims
- Application Information
AI Technical Summary
Problems solved by technology
Method used
Image
Examples
Embodiment 1
[0036] Send the mixture of methylcyclohexane and cyclohexane into the first dehydrogenation reactor 1 at a temperature of 240°C, a pressure of 0MPa, and a space velocity of 5h -1 , the catalyst is PtFeCo / Al 2 o 3 Pass through the catalyst bed under the conditions of the above conditions, the conversion rate of methylcyclohexane and cyclohexane is 40%, then enter the first separator 1, and separate at a temperature of 200 ° C and a pressure of 0 MPa, and the bottom flow enters the second Dehydrogenation reactor 3, at a temperature of 280°C, a pressure of 0MPa, and a space velocity of 4h -1 , the catalyst is PtFeCo / Al 2 o 3 It passes through the catalyst bed under certain conditions, and then enters the second separator 4 together with the top stream of the first separator 1. The composition of reactants and products in the second separator 4 was measured to obtain the conversion rate, the conversion rate was 90% at 5h, and 83% at 50h. The coking rate of the catalyst was 0....
Embodiment 2
[0038] Send the mixture of methylcyclohexane and cyclohexane into the first dehydrogenation reactor 1 at a temperature of 220°C, a pressure of 0MPa, and a space velocity of 5h -1 , the catalyst is PtFeCo / Al 2 o 3 Pass through the catalyst bed under the conditions of the above conditions, the conversion rate of methylcyclohexane and cyclohexane is 38%, then enter the first separator 1, and separate at a temperature of 200 ° C and a pressure of 0 MPa, and the bottom flow enters the second Dehydrogenation reactor 3, at a temperature of 280°C, a pressure of 0MPa, and a space velocity of 4h -1 , the catalyst is PtFeCo / Al 2 o 3 It passes through the catalyst bed under certain conditions, and then enters the second separator 4 together with the top stream of the first separator 1. The composition of reactants and products in the second separator 4 was measured to obtain the conversion rate, the conversion rate was 86% at 5h, and 78% at 50h. The coking rate of the catalyst was 0....
Embodiment 3
[0040] Send the mixture of methylcyclohexane and cyclohexane into the first dehydrogenation reactor 1 at a temperature of 280°C, a pressure of 0MPa, and a space velocity of 5h -1 , the catalyst is PtFeCo / Al 2 o 3 Pass through the catalyst bed under the conditions of the above conditions, the conversion rate of methylcyclohexane and cyclohexane is 49%, and then enter the first separator 1, separate at a temperature of 200 ° C and a pressure of 0 MPa, and the bottom flow enters the second Dehydrogenation reactor 3, at a temperature of 280°C, a pressure of 0MPa, and a space velocity of 4h -1 , the catalyst is PtFeCo / Al 2 o 3 It passes through the catalyst bed under certain conditions, and then enters the second separator 4 together with the top stream of the first separator 1. The composition of reactants and products in the second separator 4 was measured to obtain the conversion rate, the conversion rate was 96% at 5h, and 80% at 50h. The coking rate of the catalyst was 1%...
PUM
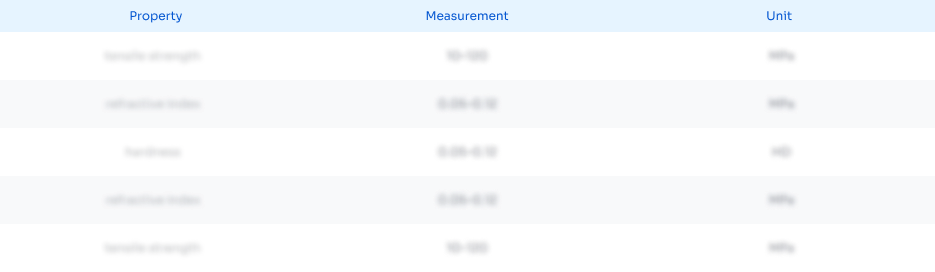
Abstract
Description
Claims
Application Information

- R&D
- Intellectual Property
- Life Sciences
- Materials
- Tech Scout
- Unparalleled Data Quality
- Higher Quality Content
- 60% Fewer Hallucinations
Browse by: Latest US Patents, China's latest patents, Technical Efficacy Thesaurus, Application Domain, Technology Topic, Popular Technical Reports.
© 2025 PatSnap. All rights reserved.Legal|Privacy policy|Modern Slavery Act Transparency Statement|Sitemap|About US| Contact US: help@patsnap.com