Hydrogenation reactor and hydrogenation method thereof
A hydrogenation reactor and reactor technology, applied in chemical instruments and methods, hydroprocessing process, hydrocarbon oil treatment, etc., can solve problems such as serious side reactions or cracking reactions, coking of catalysts, increased side reactions or cracking reactions, etc.
- Summary
- Abstract
- Description
- Claims
- Application Information
AI Technical Summary
Problems solved by technology
Method used
Image
Examples
Embodiment 1
[0043] Attached figure 1 In the method described, the catalyst used in the conical inner cylinder of the hydrogenation reactor is FHUDS-5 of the Fushun Petrochemical Research Institute, and the catalyst used in the annular space is FH-40C; the hydrogen contained in the feed of the hydrogenation reactor is used as the raw material The mass of oil (the sum of fresh raw oil and circulating oil) is 0.31%, the amount of hydrogen supplemented in the conical inner cylinder of the hydrogenation reactor is 0.24% of the mass of raw oil (the sum of fresh raw oil and circulating oil), and the amount of hydrogen in the annular space The dosage is 0.05% of the mass of the raw material oil (the sum of fresh raw material oil and circulating oil). The reaction conditions of the conical inner cylinder of the hydrogenation reactor are as follows: the reaction temperature is 300-340°C, the reaction pressure is 6.0MPaG, and the liquid hourly volume space velocity is 5.0h -1 The reaction condition...
Embodiment 2
[0046] Attached figure 1 In the method described, the catalyst used in the conical inner cylinder of the hydrogenation reactor is FHUDS-2 of Fushun Petrochemical Research Institute, and the catalyst used in the annular space is FH-40C; the hydrogen contained in the hydrogenation reactor feed is the raw material The mass of oil (the sum of fresh raw oil and circulating oil) is 0.26%, the amount of hydrogen supplemented in the conical inner cylinder of the hydrogenation reactor is 0.28% of the mass of raw oil (the sum of fresh raw oil and circulating oil), and the hydrogen in the annular space The dosage is 0.06% of the mass of feedstock oil (the sum of fresh feedstock oil and circulating oil). The reaction conditions of the conical inner cylinder of the hydrogenation reactor are as follows: the reaction temperature is 315-352°C, the reaction pressure is 6.0MPaG, and the liquid hourly volume space velocity is 4.5h -1 The reaction conditions in the annular space are as follows: ...
Embodiment 3
[0049] Attached figure 1 In the method described, the catalyst used in the conical inner cylinder of the hydrogenation reactor is FHUDS-5 of the Fushun Petrochemical Research Institute, and the catalyst used in the annular space is FHUDS-2; the hydrogen contained in the feed of the hydrogenation reactor is the raw material oil (the sum of fresh feedstock oil and circulating oil) is 0.22% of the mass, the amount of hydrogen supplemented in the conical inner cylinder of the hydrogenation reactor is 0.31% of the mass of the feedstock oil (the sum of fresh feedstock oil and circulating oil), and the supply of hydrogen in the annular space The amount is 0.07% of the mass of feedstock oil (the sum of fresh feedstock oil and circulating oil). The reaction conditions of the conical inner cylinder of the hydrogenation reactor are as follows: the reaction temperature is 318-348°C, the reaction pressure is 5.5MPaG, and the liquid hourly volume space velocity is 5.0h -1 ;The reaction con...
PUM
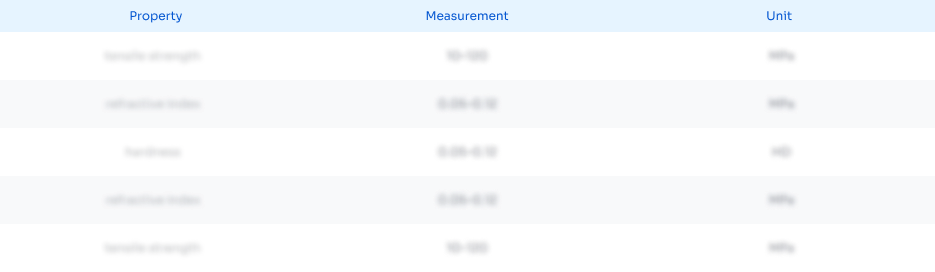
Abstract
Description
Claims
Application Information

- R&D
- Intellectual Property
- Life Sciences
- Materials
- Tech Scout
- Unparalleled Data Quality
- Higher Quality Content
- 60% Fewer Hallucinations
Browse by: Latest US Patents, China's latest patents, Technical Efficacy Thesaurus, Application Domain, Technology Topic, Popular Technical Reports.
© 2025 PatSnap. All rights reserved.Legal|Privacy policy|Modern Slavery Act Transparency Statement|Sitemap|About US| Contact US: help@patsnap.com