Multi-point parallel synchronous driving solar tracking system
A solar tracking and synchronous drive technology, applied in solar heating systems, mobile/directional solar collectors, solar thermal energy, etc., can solve problems such as inability to achieve multi-point co-locking function, inconvenient power station design, and cracking of solar modules. , to achieve the effect of improving reliability and stability, convenient operation and maintenance, and reducing jitter
- Summary
- Abstract
- Description
- Claims
- Application Information
AI Technical Summary
Problems solved by technology
Method used
Image
Examples
Embodiment 1
[0053] Such as Figure 1~4 As shown, it is a multi-point parallel synchronous drive solar tracking system, including a main shaft 3 and a plurality of columns 5 for supporting the main shaft 3, and the main shaft 3 is used for fixing solar modules 6;
[0054] It also includes a multi-point parallel synchronous driving device arranged on the main shaft 3, and the multi-point parallel synchronous driving device includes a drive mechanism 1 and several stages of driven mechanisms 2 connected by transmission;
[0055] The first power output end of the drive mechanism 1 is rotationally connected to the main shaft 3, and the main shaft 3 is used as the power output shaft; the second power output end of the drive mechanism 1 is fixed below the main shaft 3 and is axially parallel to the main shaft 3;
[0056] Several stages of the driven mechanism 5 are arranged at intervals along the main shaft 3, the second power output end of the driving mechanism 1 is connected to the power input...
Embodiment 2
[0061] Such as Figure 1~4 As shown, it is a multi-point parallel synchronous drive solar tracking system, including a main shaft 3 and a plurality of columns 5 for supporting the main shaft 3, and the main shaft 1 is used for fixing solar modules 6;
[0062] It also includes a multi-point parallel synchronous driving device arranged on the main shaft 3, and the multi-point parallel synchronous driving device includes a drive mechanism 1 and several stages of driven mechanisms 2 connected by transmission;
[0063] The first power output end of the drive mechanism 1 is rotationally connected to the main shaft 3, and the main shaft 3 is used as the power output shaft; the second power output end of the drive mechanism 1 is arranged below the main shaft 3 and is axially parallel to the main shaft 3;
[0064] The drive mechanism 1 includes a worm gear transmission unit I10 fixed on the column 5, and a transmission gear 11 as a second power output end; the worm gear transmission un...
Embodiment 3
[0082] In this embodiment, on the basis of Embodiment 1 or 2, it should be noted that, in addition to the column 5 that supports the main shaft 3, the driving mechanism 1 and the driven mechanism 2 synchronously, other columns that independently support the main shaft can also be provided. 5. Such as Figure 5a , 5b As shown, the top of this type of column 5 is fixedly connected with the column top seat 52; the main shaft 3 is passed through the bearing, and the bearing is installed in the bearing race 30; the column top seat 52 is connected with the bearing race 30 is fixedly connected to realize the rotatable support directly to the main shaft 3. In practical application, the top of the column 5 is provided with an up and down adjustable row of holes IIIC, the column top 51 is set as a U-shaped bending part, and a set of fixing holes IIID are arranged oppositely on the two vertical surfaces of the column top 51 The relative height adjustment of the column 5 and the column...
PUM
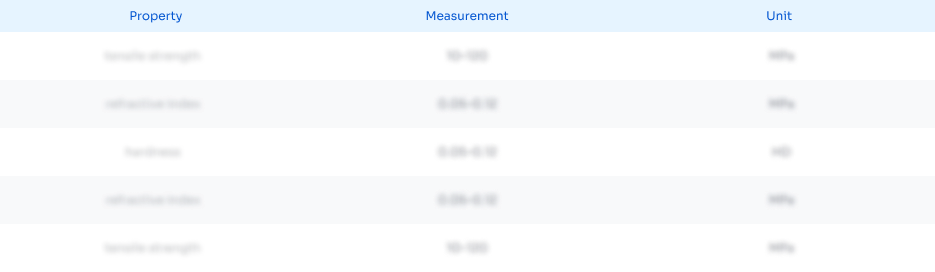
Abstract
Description
Claims
Application Information

- Generate Ideas
- Intellectual Property
- Life Sciences
- Materials
- Tech Scout
- Unparalleled Data Quality
- Higher Quality Content
- 60% Fewer Hallucinations
Browse by: Latest US Patents, China's latest patents, Technical Efficacy Thesaurus, Application Domain, Technology Topic, Popular Technical Reports.
© 2025 PatSnap. All rights reserved.Legal|Privacy policy|Modern Slavery Act Transparency Statement|Sitemap|About US| Contact US: help@patsnap.com