Method for designing large-span open-section cabin space truss structure
A space truss and structural design technology, applied in design optimization/simulation, special data processing applications, instruments, etc., can solve problems such as complex force transmission paths, large weight costs, and complex connection forms
- Summary
- Abstract
- Description
- Claims
- Application Information
AI Technical Summary
Problems solved by technology
Method used
Image
Examples
Embodiment Construction
[0024] The present invention will be described in detail below.
[0025] It is known that the torque load is 1,000kN*m, the structural material is aluminum alloy (elastic modulus 71000MPa), the stress is controlled within 400MPa, and the relative deformation of two points on the opening edge of the space truss structure section does not exceed 40mm. In this embodiment, a method for designing a space truss structure of a large-span open-section cabin is provided, which specifically includes the following contents:
[0026] step 1: figure 1 is the force analysis diagram of the actual space truss structure, combined with figure 1 As shown, according to the actual space truss structure load situation, the load is decomposed and simplified, and it is determined that the space truss structure bears the transverse shear couple and the vertical shear couple; The ability of the shear couple is strong, but the ability to withstand the transverse shear couple is weak. By designing the ...
PUM
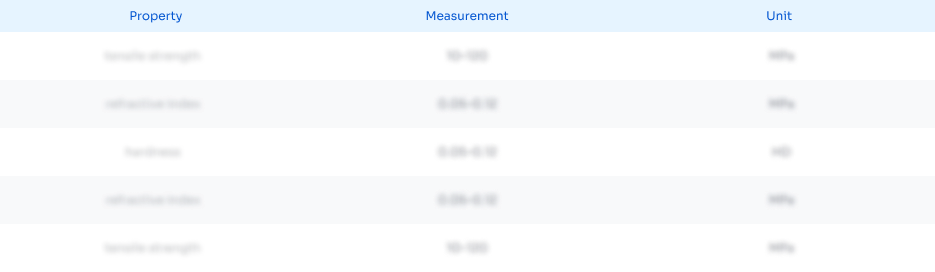
Abstract
Description
Claims
Application Information

- Generate Ideas
- Intellectual Property
- Life Sciences
- Materials
- Tech Scout
- Unparalleled Data Quality
- Higher Quality Content
- 60% Fewer Hallucinations
Browse by: Latest US Patents, China's latest patents, Technical Efficacy Thesaurus, Application Domain, Technology Topic, Popular Technical Reports.
© 2025 PatSnap. All rights reserved.Legal|Privacy policy|Modern Slavery Act Transparency Statement|Sitemap|About US| Contact US: help@patsnap.com