Method for recovering F21 and F22 from F22 rectification residual liquid
A technology of F21 and raffinate, applied in the disproportionation separation/purification of halogenated hydrocarbons, organic chemistry, etc., can solve the problems of excessive water content, increased energy consumption, increased material consumption, etc.
- Summary
- Abstract
- Description
- Claims
- Application Information
AI Technical Summary
Problems solved by technology
Method used
Examples
Embodiment 1
[0034] Example 1: Step 1: Cool the raffinate in the raffinate storage tank to 8°C; Step 2: Control the top temperature of the crude product tower to 0°C, the temperature of the bottom of the tower to 45°C, and the pressure of the tower to 1.0 MPa; Step 3: Use a molecular sieve dryer , silica gel drier to dehydrate the crude product; Step 4: Control the top temperature of the F22 separation tower to -10°C, the temperature of the tower kettle to 40°C, and the pressure at the top of the tower to 0.8MPa; Step 5: Use a molecular sieve drier to dehydrate the crude product, the The water content in F22 is 8ppm, the content in F21 is 32ppm, and the content in F22 is 99.95%; the water content in F21 is 45ppm.
Embodiment 2
[0035]Example 2: Step 1: Cool the raffinate in the raffinate storage tank to 5°C; Step 2: Control the top temperature of the crude product tower to -10°C, the temperature of the tower kettle to 35°C, and the tower pressure to 1.2MPa; Step 3: Use freeze dehydration , Molecular sieve drier, and silica gel drier to dehydrate the crude product; Step 4: Control the top temperature of the F22 separation tower to -15°C, the temperature of the tower kettle to 35°C, and the pressure at the top of the tower to 1.1MPa; Step 5: Use the molecular sieve drier and silica gel to dry The device performs circulating dehydration.
[0036] The moisture content in the recovered F22 is 5ppm, the F21 content is 25ppm, and the F22 content is 99.99%; the moisture content in the F21 is 35ppm.
Embodiment 3
[0037] Example 3: Step 1: Cool the raffinate in the raffinate storage tank to 2°C; Step 2: Control the top temperature of the crude product tower to -15°C, the temperature of the tower kettle to 30°C, and the tower pressure to 1.5MPa; Step 3: Use freeze dehydration , Molecular sieve drier, and silica gel drier to dehydrate the crude product; Step 4: Control the top temperature of the F22 separation tower to -18°C, the temperature of the tower kettle to 20°C, and the pressure at the top of the tower to 1.2MPa; Step 5: Use the molecular sieve drier to perform circular dehydration , the moisture content in the recovered F22 is 6ppm, the F21 content is 35ppm, and the F22 content is 99.98%; the moisture content in the F21 is 41ppm.
PUM
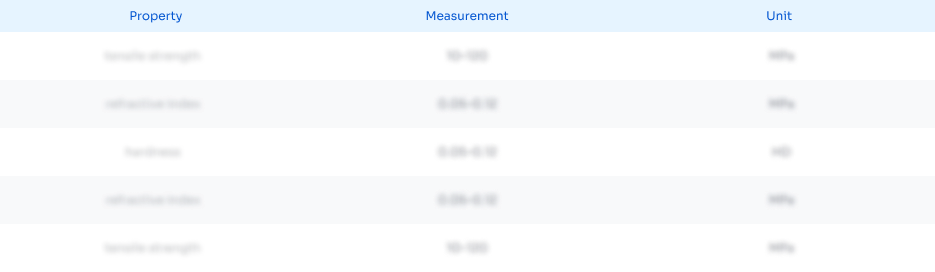
Abstract
Description
Claims
Application Information

- Generate Ideas
- Intellectual Property
- Life Sciences
- Materials
- Tech Scout
- Unparalleled Data Quality
- Higher Quality Content
- 60% Fewer Hallucinations
Browse by: Latest US Patents, China's latest patents, Technical Efficacy Thesaurus, Application Domain, Technology Topic, Popular Technical Reports.
© 2025 PatSnap. All rights reserved.Legal|Privacy policy|Modern Slavery Act Transparency Statement|Sitemap|About US| Contact US: help@patsnap.com