Manufacturing process of anti-rust metal stoving varnish
A technology of metal baking paint and manufacturing process, which is applied to the device and coating of the surface coating liquid, which can solve the problems of low efficiency, difficulty in ensuring the quality consistency of manual operation, time-consuming and labor-intensive problems, etc.
- Summary
- Abstract
- Description
- Claims
- Application Information
AI Technical Summary
Problems solved by technology
Method used
Image
Examples
Embodiment Construction
[0026] Please refer to figure 1 and figure 2 Shown, a kind of manufacturing process of anti-rust metal baking varnish comprises the steps:
[0027] Step 1. Prepare a metal sheet made of stainless steel, punch the metal sheet to form a metal mesh, then cut the metal mesh to obtain a single mesh sheet, and bend the single mesh sheet to form a workpiece with a predetermined product shape;
[0028] Step 2: Dedust and purify the surface of the predetermined shape product;
[0029] Step 3: Use the first shielding fixture to shield the first region 10 of the workpiece, the first region 10 is provided with a cavity and the wall of the cavity is provided with through holes; the surface of the unshielded second region 20 is sprayed with primer , anti-rust pigments are added in the primer;
[0030] Step 4: Use the first shielding fixture to shield the first area 10 of the workpiece, and spray the topcoat on the primer surface of the unshielded second area 20;
[0031] Step 5: Take o...
PUM
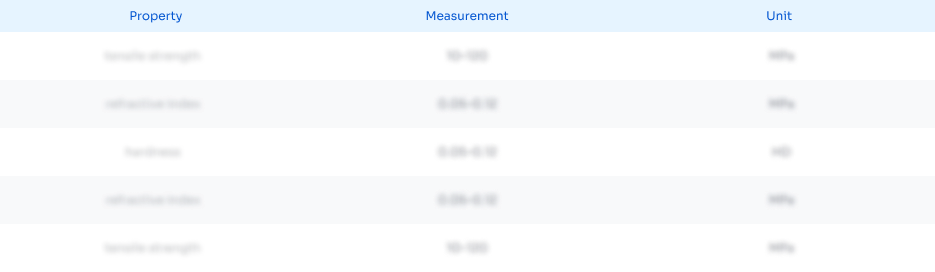
Abstract
Description
Claims
Application Information

- R&D
- Intellectual Property
- Life Sciences
- Materials
- Tech Scout
- Unparalleled Data Quality
- Higher Quality Content
- 60% Fewer Hallucinations
Browse by: Latest US Patents, China's latest patents, Technical Efficacy Thesaurus, Application Domain, Technology Topic, Popular Technical Reports.
© 2025 PatSnap. All rights reserved.Legal|Privacy policy|Modern Slavery Act Transparency Statement|Sitemap|About US| Contact US: help@patsnap.com