Anti-collision self-protection precast concrete component
A technology of prefabricated components and concrete, which is applied in basic structure engineering, construction, excavation, etc. It can solve the problems of poor concrete vibrating and compacting effect, easy to be damaged, and increased number of repeated uses.
- Summary
- Abstract
- Description
- Claims
- Application Information
AI Technical Summary
Problems solved by technology
Method used
Image
Examples
Embodiment 1
[0070] The first step: process the steel bars of the prefabricated components, use edge protectors and auxiliary tools to integrate the steel bars into a reinforcement cage, and put them into the installed mold for making prefabricated components;
[0071] Step 2: Place plastic partitions between the reinforcement cages of adjacent prefabricated components, install internal embedded parts, and insert steel strands in the reinforcement cages and plastic partitions along the longitudinal direction;
[0072] The third step: pouring concrete and curing according to the set period;
[0073] Step 4: After the curing period is reached, the mold is lifted, hoisted, and the prefabricated components are transported to the stacking position to complete the production of a batch of prefabricated components.
Embodiment 2
[0075] The first step: first complete the construction of the foundation pit column piles and columns, and at the same time as the construction of the foundation pit surrounding protection piles, pour concrete cushions at the positions of the columns (single-span without columns) and the connection point of the inner support;
[0076] Step 2: The horizontal support of the inner support frame includes support supports and mid-span supports. First, hoist and install support supports, and then install mid-span supports between two adjacent support supports. The supports are made of prefabricated panels. The parts are combined by rigid bolts;
[0077] Step 3: In the direction of the longitudinal axis of the support, the adjacent prefabricated panels are connected by longitudinal connectors, and the longitudinal connectors of the longitudinal connectors are placed into the storage holes by placing the body, and then the adjacent prefabricated panels are connected by the locking body...
Embodiment 3
[0081] What differs from embodiment 2 is the 3rd step and the 5th step:
[0082] Step 3: In the direction of the longitudinal axis of the support, the outsourcing bolts are used to connect adjacent prefabricated panels. Medium support; according to the needs, set the vertical prefabricated panel surface and the bolt body of the outer bolt plate to fix the outer bolt; if it is necessary to set measures to adjust the internal force and deformation of the support, reserve space between adjacent prefabricated panels , into the steel backing plate and the axial pressure regulator;
[0083] Step 5: After the construction of the foundation floor is completed, remove the last support, use temporary vertical support measures such as mobile support frames or scaffolding, erect it under the horizontal inner support composed of prefabricated panels, and remove the outer bolts and rigid bolts , using tower cranes or other hoisting equipment to lift the prefabricated panels out of the foun...
PUM
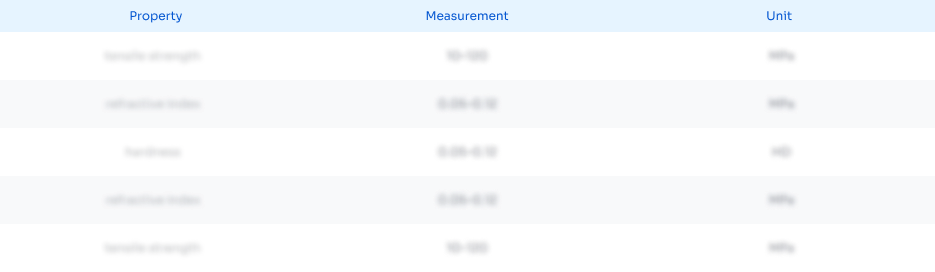
Abstract
Description
Claims
Application Information

- R&D
- Intellectual Property
- Life Sciences
- Materials
- Tech Scout
- Unparalleled Data Quality
- Higher Quality Content
- 60% Fewer Hallucinations
Browse by: Latest US Patents, China's latest patents, Technical Efficacy Thesaurus, Application Domain, Technology Topic, Popular Technical Reports.
© 2025 PatSnap. All rights reserved.Legal|Privacy policy|Modern Slavery Act Transparency Statement|Sitemap|About US| Contact US: help@patsnap.com