Mercury ring of magnetofluid angular velocity sensor and cementing method of mercury ring
An angular velocity sensor and magnetic fluid technology, applied to devices using electric/magnetic methods, steering sensing equipment, and devices for coating liquid on the surface, etc., can solve the problem of difficult control of the amount of adhesive, leaky mercury rings, Affect the measurement accuracy and other issues, to achieve the effect of increasing the area of the bonding surface, ensuring the sealing of the bonding surface, and ensuring the measurement accuracy
- Summary
- Abstract
- Description
- Claims
- Application Information
AI Technical Summary
Problems solved by technology
Method used
Image
Examples
Embodiment
[0038] (1) Gluing preparation stage
[0039] Step S1.1, cleaning the inner cylinder, outer cylinder and electrodes to make their surfaces smooth; since air bubbles may be generated on the bonding surface during the bonding process, put the cleaned inner cylinder, outer cylinder and electrodes into high temperature In the oven, set the temperature above 80°C and bake for more than half an hour to keep the surface of each part dry;
[0040] Step S1.2, since there are air bubbles in the cement itself when mixing, put the cement in a vacuum tank and evacuate until the air pressure is lower than 10 -2 Pa, to exhaust the air bubbles in the cement.
[0041] (2) Bonding stage
[0042] Step 1, after using the dispensing needle to apply the adhesive to the inner groove of the upper electrode or the lower electrode, insert the inner cylinder vertically into the inner groove of the lower electrode;
[0043] Step 2. Tilt the inserted assembly back and forth several times, each time the ...
PUM
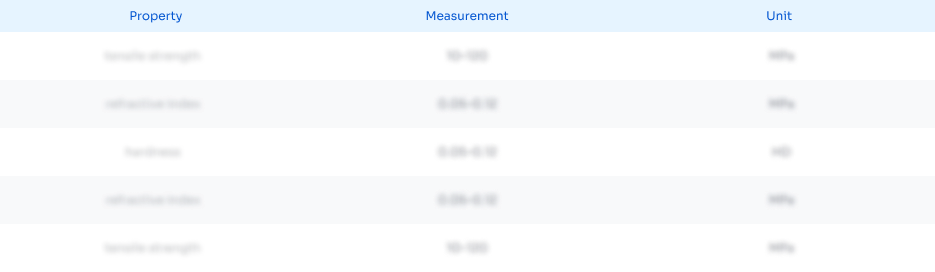
Abstract
Description
Claims
Application Information

- R&D Engineer
- R&D Manager
- IP Professional
- Industry Leading Data Capabilities
- Powerful AI technology
- Patent DNA Extraction
Browse by: Latest US Patents, China's latest patents, Technical Efficacy Thesaurus, Application Domain, Technology Topic, Popular Technical Reports.
© 2024 PatSnap. All rights reserved.Legal|Privacy policy|Modern Slavery Act Transparency Statement|Sitemap|About US| Contact US: help@patsnap.com