Steel belt feeding and discharging equipment and implementation method thereof
A steel strip and equipment technology, applied in the field of steel strip loading and unloading equipment and its realization, can solve the problems of incapable steel strip hot rolling operation, incapable steel strip adjustment, steel strip unwinding deviation, etc. The material speed is stable, ensuring no breakage, and the effect of convenient tension
- Summary
- Abstract
- Description
- Claims
- Application Information
AI Technical Summary
Problems solved by technology
Method used
Image
Examples
Embodiment 1
[0039] see Figure 1-9, the present invention provides the following technical solutions: a steel strip loading and unloading equipment, including a feeder and a feeder, the feeder includes a feeder frame 1, and the feeder frame 1 is provided with an air expansion shaft 8, The upper left corner of the air expansion shaft 8 is provided with an ultrasonic sensor 3 on the feeder frame 1, a photoelectric sensor 4 is provided on one side of the ultrasonic sensor 3, and a feeding driving roller 6 is provided on one side of the photoelectric sensor 4. The top of the material driving roller 6 is provided with a lifting roller lifting mechanism 5, the lower left corner of the feeding driving roller 6 is provided with a swinging roller mechanism 7, and several supporting rollers 2 are also provided on the feeding machine frame 1; Feeding machine frame 11, blanking machine frame 11 is provided with blanking driving roller 10, the top of blanking driving roller 10 is provided with heating...
Embodiment 2
[0047] The difference between this embodiment and Embodiment 1 is that further, the heating roller elevating mechanism 9 includes a second linear slide rail 92 and a second cylinder mounting plate 96, wherein the second linear slide rail 92 and the second cylinder mounting plate 96 Respectively installed on the blanking machine frame 11, the second cylinder mounting plate 96 is located above the second linear slide rail 92, the second cylinder mounting plate 96 is connected with the second lifting cylinder 91, the slide of the second linear slide rail 92 A heating roller mounting plate 93 is arranged on the block, and the output end of the second lift cylinder 91 is connected with the heating roller mounting plate 93. The heating roller mounting plate 93 is provided with a second main shaft 94, and the second main shaft 94 is provided with a heating roller 95.
[0048] By adopting the above technical solution, the heating roller 95 is driven to move up and down by the second li...
Embodiment 3
[0061] The difference between this embodiment and Embodiment 1 lies in that: the first main shaft 54 and the feeding driving roller 6 and the second main shaft 94 and the unloading driving roller 10 are respectively provided with corresponding gears.
[0062] By adopting the above-mentioned technical scheme, when the conveying resistance of the steel strip is large, the first lifting cylinder 51 drives the first main shaft 54 to descend so that the gears on it mesh with the gears on the feeding drive roller 6 or the second lifting cylinder 91 drives The second main shaft 94 descends to make the gear on it mesh with the gear on the blanking driving roller 10, and the first main shaft 54 is driven to rotate by the feeding driving roller 6 or the second main shaft 94 is driven by the blanking driving roller 10 to rotate, so that the steel The conveying of the belt is more stable.
[0063] Among the present invention, the ultrasonic sensor 3 selects the DS-UE28R type of Dong...
PUM
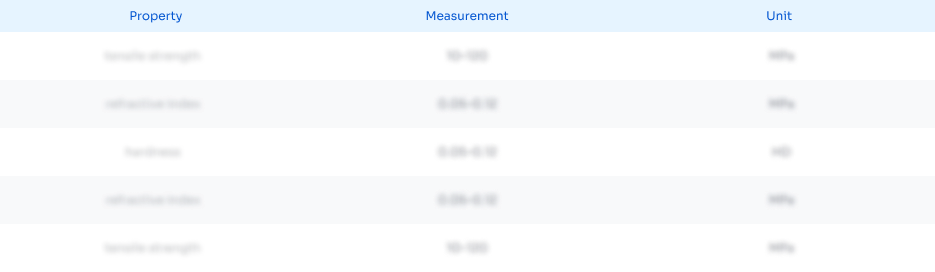
Abstract
Description
Claims
Application Information

- R&D
- Intellectual Property
- Life Sciences
- Materials
- Tech Scout
- Unparalleled Data Quality
- Higher Quality Content
- 60% Fewer Hallucinations
Browse by: Latest US Patents, China's latest patents, Technical Efficacy Thesaurus, Application Domain, Technology Topic, Popular Technical Reports.
© 2025 PatSnap. All rights reserved.Legal|Privacy policy|Modern Slavery Act Transparency Statement|Sitemap|About US| Contact US: help@patsnap.com