Rib positioning method of reinforced wallboard
A positioning method and a technology for reinforced wall panels, which are applied to household components, household appliances, other household appliances, etc., can solve the problems of affecting the qualified rate of finished products, the tendons are easily offset, and the manufacturing cost is high, so as to ensure assembly efficiency and Assembly quality, ensuring that the rib position does not deviate, and preventing the effect of rib position deviation
- Summary
- Abstract
- Description
- Claims
- Application Information
AI Technical Summary
Problems solved by technology
Method used
Image
Examples
Embodiment 1
[0028] see figure 1 , a rib positioning method for a reinforced panel, comprising the following steps:
[0029] a. Determine the position of the soft rubber mold 5 through the clamping plate. After the position of the soft rubber mold 5 is determined, mark the position of the lower backing plate 7 on the soft rubber mold 5, and mark the position of the lower backing plate 7 on the skin 1;
[0030] b. Take off the soft rubber mold 5 and the lower backing plate 7, bond the lower backing plate 7 to the soft rubber mold 5 with double-sided adhesive tape 9, and lay a layer of toughening film 8 on the skin 1, the toughening film 8 is located directly below the lower backing plate 7;
[0031] c. Assemble the combined lower backing plate 7 and rubber soft mold 5 on the skin 1 through the positioning clamp, and fill the core material 4 in the R area formed by the rubber soft mold 5 and the lower backing plate 7;
[0032] d. Use double-sided adhesive tape 9 to fix the upper backing pl...
Embodiment 2
[0035] see figure 1 , a rib positioning method for a reinforced panel, comprising the following steps:
[0036] a. Determine the position of the soft rubber mold 5 through the clamping plate. After the position of the soft rubber mold 5 is determined, mark the position of the lower backing plate 7 on the soft rubber mold 5, and mark the position of the lower backing plate 7 on the skin 1;
[0037] b. Take off the soft rubber mold 5 and the lower backing plate 7, bond the lower backing plate 7 to the soft rubber mold 5 with double-sided adhesive tape 9, and lay a layer of toughening film 8 on the skin 1, the toughening film 8 is located directly below the lower backing plate 7;
[0038] c. Assemble the combined lower backing plate 7 and rubber soft mold 5 on the skin 1 through positioning clamps, and fill the core material 4 in the R area formed by the rubber soft mold 5 and the lower backing plate 7;
[0039] d. Use double-sided adhesive tape 9 to fix the upper backing plate...
Embodiment 3
[0042] see figure 1, a rib positioning method for a reinforced panel, comprising the following steps:
[0043] a. Determine the position of the soft rubber mold 5 through the clamping plate. After the position of the soft rubber mold 5 is determined, mark the position of the lower backing plate 7 on the soft rubber mold 5, and mark the position of the lower backing plate 7 on the skin 1;
[0044] b. Take off the soft rubber mold 5 and the lower backing plate 7, bond the lower backing plate 7 to the soft rubber mold 5 with double-sided adhesive tape 9, and lay a layer of toughening film 8 on the skin 1, the toughening film 8 is located directly below the lower backing plate 7;
[0045] c. Assemble the combined lower backing plate 7 and rubber soft mold 5 on the skin 1 through the positioning clamp, and fill the core material 4 in the R area formed by the rubber soft mold 5 and the lower backing plate 7;
[0046] d. Use double-sided adhesive tape 9 to fix the upper backing pla...
PUM
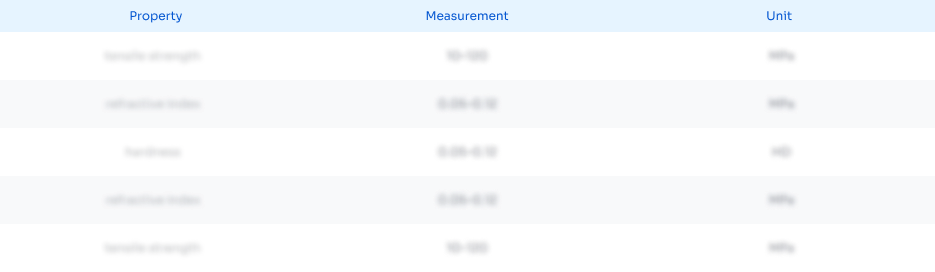
Abstract
Description
Claims
Application Information

- R&D
- Intellectual Property
- Life Sciences
- Materials
- Tech Scout
- Unparalleled Data Quality
- Higher Quality Content
- 60% Fewer Hallucinations
Browse by: Latest US Patents, China's latest patents, Technical Efficacy Thesaurus, Application Domain, Technology Topic, Popular Technical Reports.
© 2025 PatSnap. All rights reserved.Legal|Privacy policy|Modern Slavery Act Transparency Statement|Sitemap|About US| Contact US: help@patsnap.com