Power system of single-rotor helicopter without reactive torque tail rotor
A power system and anti-torque technology, which is applied in the direction of rotorcraft, aircraft power transmission, aircraft power plant, etc., can solve the problems of complex double rotor mechanism, flight speed limitation, and large tail rotor noise.
- Summary
- Abstract
- Description
- Claims
- Application Information
AI Technical Summary
Problems solved by technology
Method used
Image
Examples
Embodiment 1
[0034] A power system for a single-rotor helicopter with no counter-torque tail rotor, which consists of a body, an engine, a paddleless torque balancer, a single rotor, the body is connected to the engine, and the upper part of the engine is connected to the transmission mechanism. The above is the prior art For helicopters, the lower part of the engine (F) is connected to a combined speed reducer (ZH), and the combined speed reducer (ZH) has one to five rotor shafts (YZ) that rotate in the opposite direction to the rotor shaft (YZ). The output shaft of the axis, the output shaft of the combined reducer (ZH) is connected to the load mechanism with the same casing, and the casing (A) of the combined reducer is connected to the body (JT) and connected to the body (JT) form a relative equilibrium torque.
Embodiment 2
[0036] The power system of a single-rotor non-reactive-torque tail rotor helicopter described in embodiment 1, the combined speed reducer (ZH) is composed of a planetary speed reduction unit and a parallel shaft speed reduction unit, and the first to five The root power output shaft is centered on the middle gear in the parallel shaft reduction unit, and its peripheral teeth are evenly distributed at 360 degrees to engage with one to five output gears or output gear sets, and the output gears or output gear sets are connected to the output shaft , based on the principle that its rotation direction is opposite to the rotation direction of the rotor shaft (YZ), taking the combined double-shaft output reducer (ZH) included in the combined reducer as an example: the lower output shaft (1) of the engine is connected to the combined double-shaft The sun gear (2) of the output reducer, the sun gear (2) is connected to at least three star gears (3-3) at 120 degrees to each other, and t...
Embodiment 3
[0038] The power system of a single-rotor non-reverse torque tail rotor helicopter described in embodiment 1 or 2, the load mechanism includes: a radial plunger mechanism (J) in the medium pressure technology, and a radial plunger mechanism (J) in the power transmission technology. Various clutches, couplers, coupling couplings, disc brake mechanisms (D) in brake technology, or combined load mechanisms (DJ) composed of two of them, with one of the above load mechanisms Institutions come to specific applications,
[0039]Concrete application of radial injection plug type load mechanism (J) in this helicopter power system: one, on the described combined type biaxial output reducer housing (A) with output shaft (Z16), (Z12) as At least two cylinders (24-4) are evenly distributed in the center, and the plunger (22-4) is slidably connected in the cylinder (24-4), and the inner top of the cylinder (24-4) is connected with the plunger (22-4). ) is connected to the spring (23-4) betw...
PUM
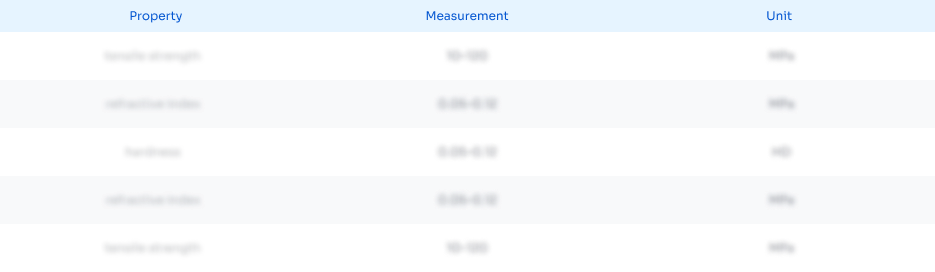
Abstract
Description
Claims
Application Information

- R&D
- Intellectual Property
- Life Sciences
- Materials
- Tech Scout
- Unparalleled Data Quality
- Higher Quality Content
- 60% Fewer Hallucinations
Browse by: Latest US Patents, China's latest patents, Technical Efficacy Thesaurus, Application Domain, Technology Topic, Popular Technical Reports.
© 2025 PatSnap. All rights reserved.Legal|Privacy policy|Modern Slavery Act Transparency Statement|Sitemap|About US| Contact US: help@patsnap.com