Electrolytic copper foil surface processor and working method thereof
A technology of surface treatment machine and electrolytic copper foil, which is applied in the direction of electrolytic process, electrolytic components, dry cargo handling, etc. It can solve the problems of electrolytic copper foil not up to standard, excessive traction force, and change of residence time, so as to improve electroplating efficiency and improve Production quality, smoothness improvement effect
- Summary
- Abstract
- Description
- Claims
- Application Information
AI Technical Summary
Problems solved by technology
Method used
Image
Examples
Embodiment Construction
[0034] Such as Figure 1-11 As shown, the present invention discloses an electrolytic copper foil surface treatment machine, which is mainly composed of an uncoiling device 1, an intermediate treatment tank section 2, a drying box 3, a winding device 4 and a control device. The intermediate treatment tank section 2 Including: a frame 21, a plurality of processing devices 22 arranged on the frame 21, and a tension roller 232 mechanism 23 arranged between adjacent processing devices 22; the processing device 22 includes a processing tank 221, a conductive Device 222, water squeezing device 223, synchronous belt transmission mechanism 224, drive motor reducer 225 are formed, and described processing tank 221 is installed in frame 21, and the liquid roller 2213 in processing tank 221 stretches out processing tank 221 part and passes bearing The seat 2221 is fixed on the frame 21, the conductive device 222 is installed on the frame 21 on both sides above the treatment tank 221, the...
PUM
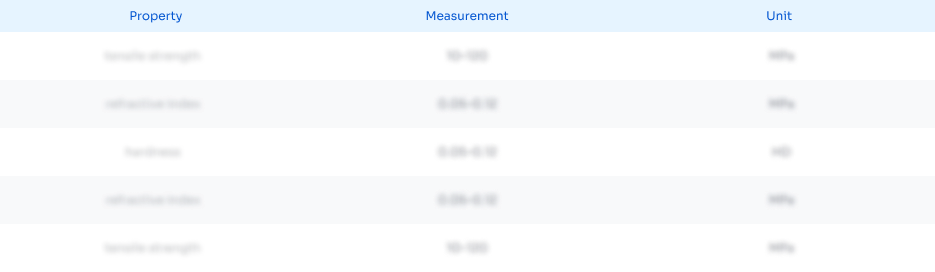
Abstract
Description
Claims
Application Information

- Generate Ideas
- Intellectual Property
- Life Sciences
- Materials
- Tech Scout
- Unparalleled Data Quality
- Higher Quality Content
- 60% Fewer Hallucinations
Browse by: Latest US Patents, China's latest patents, Technical Efficacy Thesaurus, Application Domain, Technology Topic, Popular Technical Reports.
© 2025 PatSnap. All rights reserved.Legal|Privacy policy|Modern Slavery Act Transparency Statement|Sitemap|About US| Contact US: help@patsnap.com