Multifunctional necking machine
A multi-functional, shrinking technology, applied in the field of shrinking machines, can solve the problems of inability to apply force to the pipeline, concave lines, extrusion, etc., and achieve the effect of reducing surface friction and avoiding overfitting.
- Summary
- Abstract
- Description
- Claims
- Application Information
AI Technical Summary
Problems solved by technology
Method used
Image
Examples
Embodiment 1
[0025] as attached figure 1 to attach Figure 5 Shown:
[0026] The invention provides a multifunctional necking machine, the structure of which comprises a necking device 1, a mounting base 2, a control panel 3, and a motor 4. The necking device 1 is bolted directly above the mounting base 2, and the mounting base 2. The outer end surface is connected to the control panel 3 by welding, and the control panel 3 is embedded and installed directly under the motor 4, and the motor 4 is embedded and installed on the left side of the necking device 1; the necking device 1 It includes a clamping mechanism 11, an inlay plate 12, a gear rod 13, a power shaft 14, and an embedded seat 15. The clamping mechanism 11 is inlaid and installed on the left side of the inlay plate 12, and the right end surface of the inlay plate 12 is Connected to the gear rod 13, the gear rod 13 is engaged with the power shaft 14, the power shaft 14 is located on the right side of the clamping mechanism 11, a...
Embodiment 2
[0033] as attached Figure 6 to attach Figure 7 As shown: the extension device 131 includes a chute 311, a limit shaft 312, a movable shaft 313, an elastic rope 314, and an extension plate 315. The bit shaft 312 is located on the left side of the movable shaft 313, and the movable shaft 313 is movably mounted on the inner upper end surface of the extension device 131, and the left end surface of the elastic rope 314 is embedded and connected to the left side of the extension plate 315. Below, the extension plate 315 is movably connected to the limit shaft 312. The outer contour of the extension plate 315 is arc-shaped, and the distance from the small end of the left upper surface is a plane. When the extension plate 315 is squeezed , can slide to the left port in the sliding groove 311 to extend the extrusion area.
[0034] Wherein, the extension plate 315 includes a second inlay groove 151, an inlay plate 152, a second chute 153, and a movable plate 154. The second inlay gro...
PUM
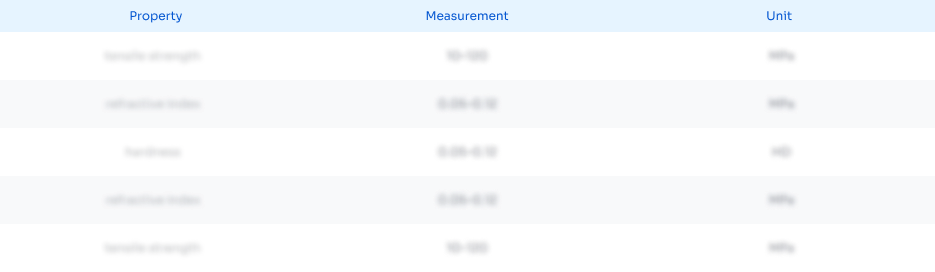
Abstract
Description
Claims
Application Information

- R&D Engineer
- R&D Manager
- IP Professional
- Industry Leading Data Capabilities
- Powerful AI technology
- Patent DNA Extraction
Browse by: Latest US Patents, China's latest patents, Technical Efficacy Thesaurus, Application Domain, Technology Topic, Popular Technical Reports.
© 2024 PatSnap. All rights reserved.Legal|Privacy policy|Modern Slavery Act Transparency Statement|Sitemap|About US| Contact US: help@patsnap.com