Wafer cutting method
A cutting method and wafer technology, applied in semiconductor/solid-state device testing/measurement, electrical components, circuits, etc., can solve problems such as splits, cracks, insufficient cutting time, etc., and achieve the effect of precise control of cutting amount
- Summary
- Abstract
- Description
- Claims
- Application Information
AI Technical Summary
Problems solved by technology
Method used
Image
Examples
Embodiment Construction
[0019] The wafer cutting method of the present invention is mainly aimed at wafer ring cutting. According to the principle of cutting, the heat in the cutting area is accumulated due to the severe friction between the cutting head and the wafer during cutting, and the temperature continues to rise. sudden change in temperature. like figure 1 As shown, the entire cutting system includes a cutting head, which realizes the circular cutting action of the wafer, and also includes a thermal sensing module, a signal processing unit, a data processing unit and a feedback signal circuit. When the wafer is circumferentially cut by the dicing unit, a thermal sensing module is arranged under the wafer. Specifically, after the wafer is adsorbed on the cutting table, the thermal module is installed at the position directly below the wafer radius of 130-150mm. The thermal module and the cutting head are placed opposite to each other on both sides of the wafer. The number of thermal modules...
PUM
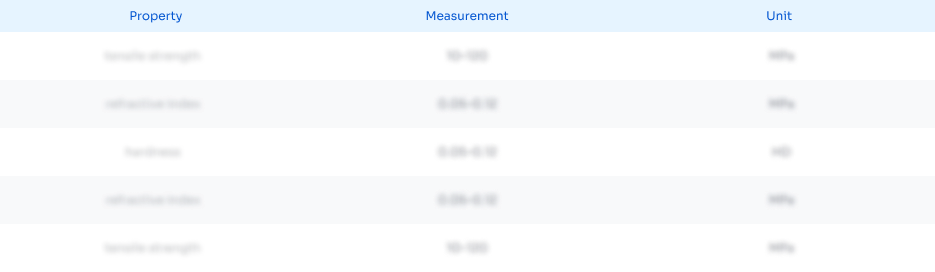
Abstract
Description
Claims
Application Information

- Generate Ideas
- Intellectual Property
- Life Sciences
- Materials
- Tech Scout
- Unparalleled Data Quality
- Higher Quality Content
- 60% Fewer Hallucinations
Browse by: Latest US Patents, China's latest patents, Technical Efficacy Thesaurus, Application Domain, Technology Topic, Popular Technical Reports.
© 2025 PatSnap. All rights reserved.Legal|Privacy policy|Modern Slavery Act Transparency Statement|Sitemap|About US| Contact US: help@patsnap.com