Machine tool complete machine static rigidity design method
A design method, static stiffness technology, applied in the field of machine tools
- Summary
- Abstract
- Description
- Claims
- Application Information
AI Technical Summary
Problems solved by technology
Method used
Image
Examples
Embodiment Construction
[0054] In order to further understand the invention content, characteristics and effects of the present invention, the following examples are given, and detailed descriptions are as follows in conjunction with the accompanying drawings:
[0055] Such as figure 1 As shown, a static stiffness design method for machine tools includes semi-analytical modeling and matching design for machine tool static stiffness. The contribution of the elasticity of the part to the stiffness of the end is used for matching design. Specifically include the following steps:
[0056] step 1, figure 2 It shows a schematic diagram of a machine tool with a topological structure, which can be abstracted into a tree-structured topology model, such as image 3 as shown ( image 3 middle, F T is the six-dimensional external load at the reference point at the end of the tool chain; F W is the six-dimensional external load at the reference point at the end of the workpiece chain; is a fixed coordina...
PUM
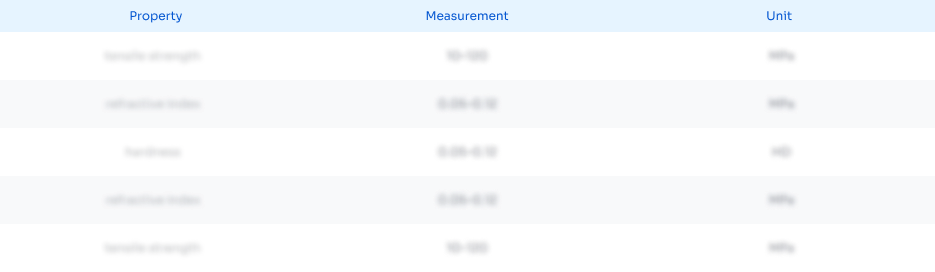
Abstract
Description
Claims
Application Information

- R&D Engineer
- R&D Manager
- IP Professional
- Industry Leading Data Capabilities
- Powerful AI technology
- Patent DNA Extraction
Browse by: Latest US Patents, China's latest patents, Technical Efficacy Thesaurus, Application Domain, Technology Topic, Popular Technical Reports.
© 2024 PatSnap. All rights reserved.Legal|Privacy policy|Modern Slavery Act Transparency Statement|Sitemap|About US| Contact US: help@patsnap.com