A comprehensive recovery method for flotation of silver concentrate with zinc hydrometallurgy acid leaching slag
A technology of acid leaching and wet zinc smelting, which is applied in the direction of chemical instruments and methods, iron compounds, process efficiency improvement, etc., can solve problems such as the preparation of iron phosphate that has not been seen, and achieve the reduction of outsourcing, simple and easy process, The effect of reducing production costs
- Summary
- Abstract
- Description
- Claims
- Application Information
AI Technical Summary
Problems solved by technology
Method used
Image
Examples
Embodiment 1
[0042] A. Activated reduction dezincification: mix the silver concentrate pulp obtained by flotation of the acid leaching residue of hydrometallurgy zinc and the zinc electrolysis waste liquid in the leaching tank at a volume ratio of 1:1.2, and place the plate with pinholes at the bottom of the leaching tank. The flue gas after roasting in the boiling furnace of zinc concentrate and after dust collection treatment is slowly introduced into the pipe, the dezincification temperature is 90 °C, the dezincification time is 12 hours, and the amount of sulfur dioxide introduced is 0.8 × 10 -2 mol / g, Mn in zinc electrolysis waste solution 2+ The content is 12g / L, and the end point acidity is 10g / L.
[0043] B, goethite method for iron precipitation: use the leaching solution obtained in step A to use goethite method for iron precipitation, the oxidant is oxygen, pH=2.5, and Fe in the solution after iron precipitation 全 =3g / L, the end point of sinking iron is Fe 2+ It is 1.0g / L, the...
Embodiment 2
[0048] A. Activated reduction dezincification: Mix the silver concentrate slurry obtained by flotation of the acid leaching residue of hydrometallurgy zinc and the zinc electrolysis waste liquid in the leaching tank at a volume ratio of 1:1.8, and place the plate with pinholes at the bottom of the leaching tank. The flue gas after roasting in the boiling furnace of zinc concentrate and after dust collection is slowly passed into the pipe, the dezincification temperature is 75℃, the dezincification time is 3 hours, and the amount of sulfur dioxide introduced is 2.5×10 -2 mol / g, Mn in zinc electrolysis waste solution 2+ The content is 4g / L, and the endpoint acidity is controlled at 25g / L.
[0049] B, goethite method for iron precipitation: use the leaching solution obtained in step A to use goethite method for iron precipitation, the oxidant is air, pH=2.8, and Fe in the liquid after iron precipitation 全 =5g / L, the end point of immersed iron is Fe 2+ It is 2.4g / L, the temperat...
Embodiment 3
[0054] A. Activated reduction dezincification: Mix the silver concentrate pulp obtained by the flotation of the acid leaching residue of hydrometallurgy zinc and the zinc electrolysis waste liquid in the leaching tank in a volume ratio of 1:1.5, and place a plate with pinholes at the bottom of the leaching tank. The flue gas after roasting in the boiling furnace of zinc concentrate and after dust collection treatment is slowly passed into the pipe, the dezincification temperature is 80 °C, the dezincification time is 6 hours, and the amount of sulfur dioxide introduced is 1.5 × 10 -2 mol / g, Mn in zinc electrolysis waste solution 2+ The content is 8g / L, and the end point acidity is controlled at 15g / L.
[0055] B, goethite method for iron precipitation: use the leaching solution obtained in step A to use goethite method for iron precipitation, the oxidant is 7 air, pH=2.7, and Fe in the liquid after the iron precipitation 全 =4g / L, the end point of immersed iron is Fe 2+ It is...
PUM
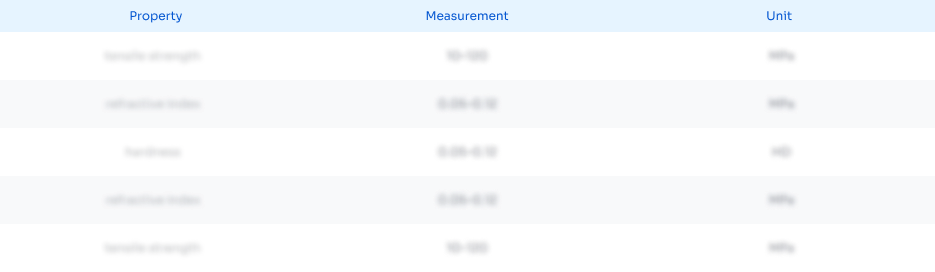
Abstract
Description
Claims
Application Information

- R&D Engineer
- R&D Manager
- IP Professional
- Industry Leading Data Capabilities
- Powerful AI technology
- Patent DNA Extraction
Browse by: Latest US Patents, China's latest patents, Technical Efficacy Thesaurus, Application Domain, Technology Topic, Popular Technical Reports.
© 2024 PatSnap. All rights reserved.Legal|Privacy policy|Modern Slavery Act Transparency Statement|Sitemap|About US| Contact US: help@patsnap.com