Method for remanufacturing semi-finishing milling cutter by using abandoned finishing milling cutter
A technology of semi-finishing milling and wheel grooves, which is applied in the field of remaking semi-finishing milling cutters from scrap fine milling cutters, and can solve the problems of high consumption of semi-finishing milling cutters.
- Summary
- Abstract
- Description
- Claims
- Application Information
AI Technical Summary
Problems solved by technology
Method used
Image
Examples
specific Embodiment approach 1
[0010] Specific implementation mode one: combine Figure 1 to Figure 7 Describe this implementation mode, this implementation mode is realized through the following steps:
[0011] Step 1. Determine the machining allowance, and inspect each groove fine milling cutter 1 to be modified on the magnifying instrument to ensure that the single-sided size of the standard groove semi-finish milling cutter profile II is smaller than the groove fine milling cutter to be modified The single-sided size of profile I of 1 is 0.2 mm, that is, the single-sided machining allowance of profile I of the wheel groove fine milling cutter 1 to be modified is greater than 0.2 mm, so as to determine that the wheel groove fine milling cutter 1 to be modified has enough Grinding the remaining amount, so that the outline dimension of the modified wheel groove fine milling cutter meets the machining accuracy requirements (the wheel groove semi-finishing milling cutter is a tool with high precision require...
specific Embodiment approach 2
[0015] Embodiment 2: This embodiment also includes step 5. In step 5, the restructured wheel groove finish milling cutter 2 obtained in step 4 is coated with a TiAlN nanocomposite coating. The tool with this coating has high wear resistance and low coefficient of friction, which can increase the service life of the tool. Other steps and parameters are the same as in the first embodiment.
PUM
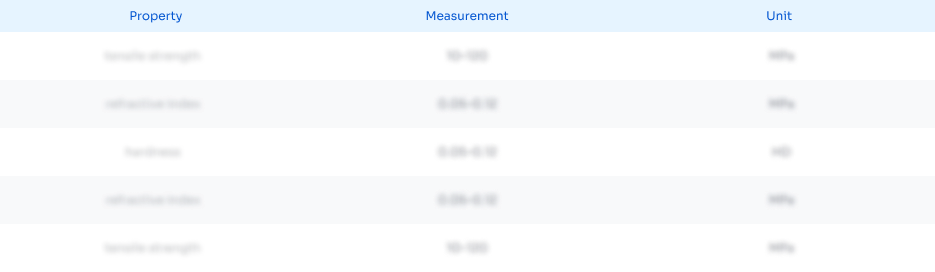
Abstract
Description
Claims
Application Information

- R&D Engineer
- R&D Manager
- IP Professional
- Industry Leading Data Capabilities
- Powerful AI technology
- Patent DNA Extraction
Browse by: Latest US Patents, China's latest patents, Technical Efficacy Thesaurus, Application Domain, Technology Topic.
© 2024 PatSnap. All rights reserved.Legal|Privacy policy|Modern Slavery Act Transparency Statement|Sitemap