Flexible assembling and welding system for standard parts and non-standard parts and method
A non-standard part, welding system technology, applied in welding equipment, welding equipment, auxiliary welding equipment, etc., can solve the problems of workpiece shape deviation, affecting physical health, and only adapting to the same workpiece clamping.
- Summary
- Abstract
- Description
- Claims
- Application Information
AI Technical Summary
Problems solved by technology
Method used
Image
Examples
Embodiment 1
[0081] A method for a flexible assembly welding system for standard parts and non-standard parts, the method includes the following steps:
[0082] Step 1: Determine the shape and size of each workpiece in standard or non-standard parts;
[0083] Step 2: After determining the shape and size of each workpiece in the standard part or non-standard part, the robotic arm of the robot 1 cooperates with the magnetic gripper assembly 101 of the positioning fixture, and grabs the rotary platform plate through the magnetic gripper assembly 101 of the positioning fixture for positioning The magnet 60, the angle rib positioning body 61, the rotary platform tube rod positioning body 62 or the above-mentioned combination are used to delineate the outline of each workpiece on the double-station flexible positioning rotary platform 4; the above-mentioned rotary platform plate positioning magnet 60, angle The rib positioning body 61, the rotary platform tube rod positioning body 62 or the comb...
Embodiment 2
[0091] A method for a flexible assembly welding system for standard parts and non-standard parts, the method includes the following steps:
[0092] Step 1: Determine the shape and size of each workpiece in standard or non-standard parts;
[0093] Step 2: After determining the shape and size of each workpiece in the standard part or non-standard part, the robotic arm of the robot 1 cooperates with the magnetic gripper assembly 101 of the positioning fixture, and grabs the rotary platform plate through the magnetic gripper assembly 101 of the positioning fixture for positioning The magnet 60, the angle rib positioning body 61, the rotary platform tube rod positioning body 62 or the above-mentioned combination are used to delineate the outline of each workpiece on the double-station flexible positioning rotary platform 4; the above-mentioned rotary platform plate positioning magnet 60, angle The rib positioning body 61, the rotary platform tube rod positioning body 62 or the comb...
Embodiment 3
[0102] A method for a flexible assembly welding system for standard parts and non-standard parts, the method includes the following steps:
[0103] Step 1: Determine the shape and size of each workpiece in standard or non-standard parts;
[0104] Step 2: After determining the shape and size of each workpiece in the standard part or non-standard part, the robotic arm of the robot 1 cooperates with the magnetic gripper assembly 101 of the positioning fixture, and grabs the rotary platform plate through the magnetic gripper assembly 101 of the positioning fixture for positioning The magnet 60, the angle rib positioning body 61, the rotary platform tube rod positioning body 62 or the above-mentioned combination are used to delineate the outline of each workpiece on the double-station flexible positioning rotary platform 4; the above-mentioned rotary platform plate positioning magnet 60, angle The rib positioning body 61, the rotary platform tube rod positioning body 62 or the comb...
PUM
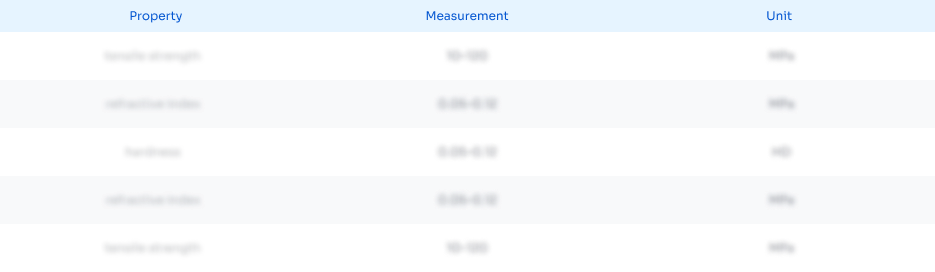
Abstract
Description
Claims
Application Information

- R&D Engineer
- R&D Manager
- IP Professional
- Industry Leading Data Capabilities
- Powerful AI technology
- Patent DNA Extraction
Browse by: Latest US Patents, China's latest patents, Technical Efficacy Thesaurus, Application Domain, Technology Topic, Popular Technical Reports.
© 2024 PatSnap. All rights reserved.Legal|Privacy policy|Modern Slavery Act Transparency Statement|Sitemap|About US| Contact US: help@patsnap.com