Beneficiation method for fine flake graphite ore
A beneficiation method and fine scale technology, applied in flotation, solid separation, grain processing, etc., can solve the problems of low flotation index and long separation process, achieve short beneficiation process, improve production efficiency, and simplify grinding and floating operations Effect
- Summary
- Abstract
- Description
- Claims
- Application Information
AI Technical Summary
Problems solved by technology
Method used
Image
Examples
Embodiment 1
[0028] (1) Fine flake graphite raw ore (grade 5%, from Panzhihua) is crushed, and the fine crushing is carried out by a high-pressure roller mill. After crushing to -1mm, it is pre-screened and inspected by a spiral classifier. It forms a section of closed-circuit grinding with the screening equipment, the material above the +0.5mm screen enters the grinding, the material under the screen (-0.074mm content is 49.52%) enters the slurry mixing tank for slurry mixing (concentration is 8%), and the slurry enters the SF type Flotation machine, add kerosene and 2 # Oil, after fully stirring, carry out roughing, the concentration of roughing is 7.08%, and the amount of kerosene is 375g / t, 2 # The amount of oil used is 55g / t to obtain rough concentrate and tailings 1;
[0029] (2) The coarse concentrate enters the ball mill for regrinding I operation, the regrinding concentration is 32.51%, the grinding fineness is -0.074mm and the content is 68.37%; the regrinding I product is sent ...
Embodiment 2
[0038] (1) The fine flake graphite raw ore (grade 4%) is crushed, and the high-pressure roller mill is used for fine crushing. After crushing to -1mm, pre-screening and inspection screening are carried out by a spiral classifier. The grinding and screening The equipment constitutes a closed-circuit grinding stage, the material on the +0.5mm screen enters the grinding, the material under the screen (-0.074mm content is 50.39%) enters the slurry tank for slurry mixing (concentration is 9%), and the pulp enters KYF / XCF flotation machine, add kerosene and 2 # Oil, after fully stirring, carry out roughing, the concentration of roughing is 8.76%, and the amount of kerosene is 370g / t, 2 # The amount of oil used is 50g / t to obtain rough concentrate and tailings 1;
[0039] (2) Coarse concentrate enters the vertical stirring mill for regrinding Ⅰ operation, the regrinding concentration is 33.58%, the grinding fineness is -0.074mm and the content is 69.79%; the regrinding Ⅰ product is ...
PUM
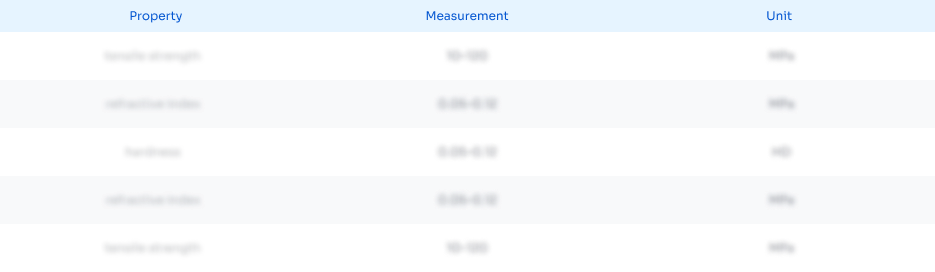
Abstract
Description
Claims
Application Information

- R&D
- Intellectual Property
- Life Sciences
- Materials
- Tech Scout
- Unparalleled Data Quality
- Higher Quality Content
- 60% Fewer Hallucinations
Browse by: Latest US Patents, China's latest patents, Technical Efficacy Thesaurus, Application Domain, Technology Topic, Popular Technical Reports.
© 2025 PatSnap. All rights reserved.Legal|Privacy policy|Modern Slavery Act Transparency Statement|Sitemap|About US| Contact US: help@patsnap.com