Manufacturing process of motor stator with locally separated tooth yokes
A technology of motor stator and partial separation, which is applied in the direction of manufacturing motor generators, manufacturing stator/rotor bodies, electrical components, etc., can solve the problems of size error, stator shape deformity, low work efficiency, etc., to facilitate transportation and measurement, avoid Dimensional error, high work efficiency effect
- Summary
- Abstract
- Description
- Claims
- Application Information
AI Technical Summary
Problems solved by technology
Method used
Image
Examples
Embodiment
[0035] Embodiment: A motor stator manufacturing process with tooth yoke partially separated, the manufacturing structure is as follows figure 1 The stator core shown, figure 1The stator core includes the base outer ring 101, the even-numbered slot yoke joint surface 4 and the odd-numbered slot yoke joint surface 3, and the manufacturing process specifically includes the following process steps:
[0036] Step A, feeding: take the strip material and send it to the punching machine, so that the strip material can be continuously fed forward on the punching machine; the punching machine is successively equipped with a punching guide hole station 10 and a punching pre-hole in the forward direction. Station 11, Punching and winding slot hole station 12, Punching odd slot tooth yoke splicing surface station 13, Punching even slot tooth yoke splicing surface station 14, Punching base measurement hole station 15, Punching tooth part measurement hole station 16. Punching inner hole sta...
PUM
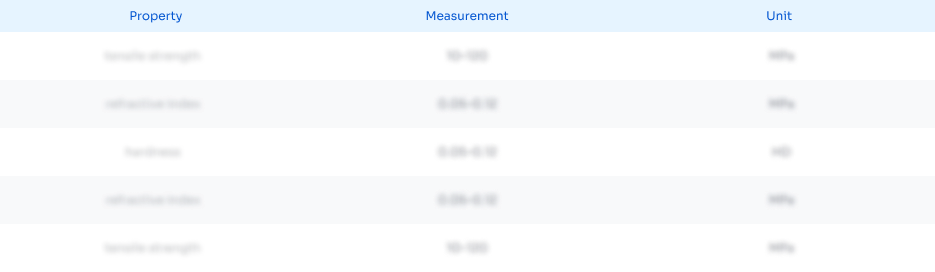
Abstract
Description
Claims
Application Information

- R&D
- Intellectual Property
- Life Sciences
- Materials
- Tech Scout
- Unparalleled Data Quality
- Higher Quality Content
- 60% Fewer Hallucinations
Browse by: Latest US Patents, China's latest patents, Technical Efficacy Thesaurus, Application Domain, Technology Topic, Popular Technical Reports.
© 2025 PatSnap. All rights reserved.Legal|Privacy policy|Modern Slavery Act Transparency Statement|Sitemap|About US| Contact US: help@patsnap.com