Rigidity-controllable supporting device and CT machine frame system
A support device and rigidity technology, applied in the field of devices that can control the support rigidity, can solve the problems of the influence of the support effect, the complex structure, the difficulty of steplessly adjusting the angle of the frame, etc., and achieve the effect of ensuring safe operation and improving the rigidity of the support.
- Summary
- Abstract
- Description
- Claims
- Application Information
AI Technical Summary
Problems solved by technology
Method used
Image
Examples
Embodiment 1
[0025]Example 1: See attachedfigure 1 As shown, a support device with controllable stiffness includes an oil cylinder 1. The oil cylinder 1 is composed of a cylinder barrel 2, a piston 3 and a piston rod 4. The inside of the cylinder barrel 2 is divided into a rod cavity 5 and a rodless cavity 6 by the piston 3 In two parts, the outer end of the cylinder at one end of the rodless cavity 6 is fixedly connected with an earring as the first connecting structure 10, and the outer end of the piston rod 4 is fixedly connected with an earring as the second connecting structure 11.
[0026]A solenoid valve 7 is provided. The first oil port of the solenoid valve 7 communicates with the rodless cavity 6 through the first pipe 8, and the second oil port of the solenoid valve 7 communicates with the rod cavity 5 through the second pipe 9. The oil port and the second oil port are controlled by the solenoid valve 7. The rod cavity 5, the rodless cavity 6, the first pipe 8 and the second pipe 9 are f...
Embodiment 2
[0029]Example 2: See attachedfigure 2 As shown, a medical CT machine frame system is composed of a base 22, a tiltable part 23, a driving part 21, and a support device 24 with controllable stiffness. Wherein, the tiltable part 23 is rotatably connected to the base 22.
[0030]SeeFigure 4The driving component 21 in this embodiment adopts a hydraulic transmission mechanism to drive the tiltable part 23 to rotate relative to the base to adjust its tilt angle. A support device 24 with controllable rigidity is provided at the other end of the frame for lifting the tiltable part. To support.
[0031]See attachedfigure 2 Andimage 3 , The frame needs to have different postures when working, the driving part 21 is used to change the frame posture, and the rigidity controllable support device 24 is used to lock the frame when the frame reaches the working posture to increase the frame rigidity.
[0032]Typical system block diagram such asFigure 4As shown, the rigidity controllable support device 24 an...
PUM
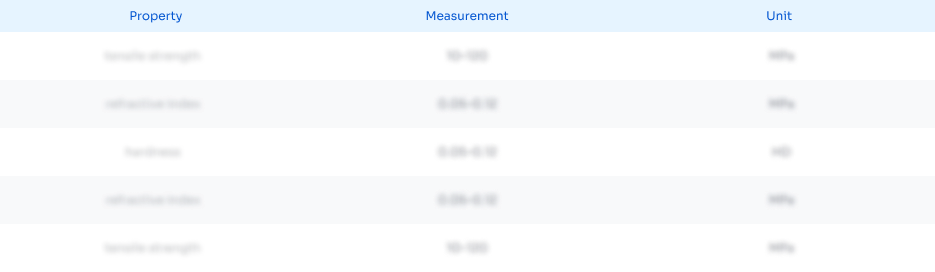
Abstract
Description
Claims
Application Information

- Generate Ideas
- Intellectual Property
- Life Sciences
- Materials
- Tech Scout
- Unparalleled Data Quality
- Higher Quality Content
- 60% Fewer Hallucinations
Browse by: Latest US Patents, China's latest patents, Technical Efficacy Thesaurus, Application Domain, Technology Topic, Popular Technical Reports.
© 2025 PatSnap. All rights reserved.Legal|Privacy policy|Modern Slavery Act Transparency Statement|Sitemap|About US| Contact US: help@patsnap.com