An Electromagnetic Quasi-Zero Stiffness Vibration Isolation System Based on Stewart Platform
A quasi-zero stiffness, vibration isolation system technology, applied in non-rotational vibration suppression, spring/shock absorber functional characteristics, spring/shock absorber, etc., can solve active vibration isolation with high energy consumption, high cost, complex structure, etc. problem, to achieve the effect of reducing the natural frequency, widening the vibration isolation frequency band, and simple structure
- Summary
- Abstract
- Description
- Claims
- Application Information
AI Technical Summary
Problems solved by technology
Method used
Image
Examples
Embodiment Construction
[0024] The following will clearly and completely describe the technical solutions in the embodiments of the present invention with reference to the accompanying drawings in the embodiments of the present invention. Obviously, the described embodiments are only some, not all, embodiments of the present invention. Based on the embodiments of the present invention, all other embodiments obtained by persons of ordinary skill in the art without making creative efforts belong to the protection scope of the present invention.
[0025] The object of the present invention is to provide an electromagnetic quasi-zero stiffness vibration isolation system based on a Stewart platform to solve the problems in the prior art above, so that the vibration isolation system can achieve quasi-zero stiffness and the vibration isolation frequency band is expanded.
[0026] In order to make the above objects, features and advantages of the present invention more comprehensible, the present invention wi...
PUM
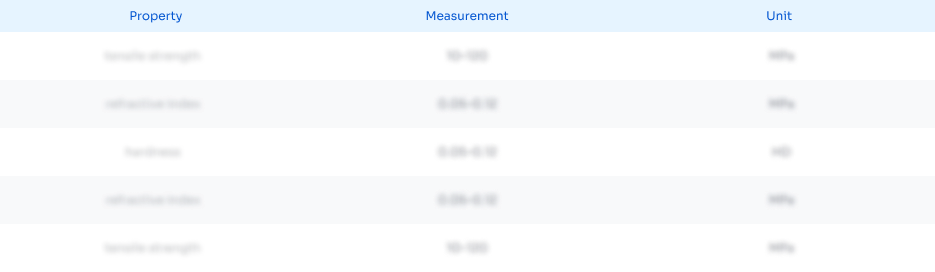
Abstract
Description
Claims
Application Information

- Generate Ideas
- Intellectual Property
- Life Sciences
- Materials
- Tech Scout
- Unparalleled Data Quality
- Higher Quality Content
- 60% Fewer Hallucinations
Browse by: Latest US Patents, China's latest patents, Technical Efficacy Thesaurus, Application Domain, Technology Topic, Popular Technical Reports.
© 2025 PatSnap. All rights reserved.Legal|Privacy policy|Modern Slavery Act Transparency Statement|Sitemap|About US| Contact US: help@patsnap.com