Self-standing compression bag and preparation process
A technology for compressing bags and bag bodies, applied in the field of packaging bags, can solve the problems of single type of compressed bags, easy rupture of compressed bags, and limited storage capacity of contents, etc., and achieve the effects of enhancing wear resistance, increasing volume, and prolonging use time.
- Summary
- Abstract
- Description
- Claims
- Application Information
AI Technical Summary
Problems solved by technology
Method used
Examples
preparation example Construction
[0026] A preparation process for a self-supporting compression bag, comprising the steps of:
[0027] Step 1: Put the raw material of the bag body in the reaction kettle to melt at high temperature, and put the melted raw material into the film blowing machine to blow out the material film;
[0028] Step 2: Place the raw material of the bag holder in a reactor for high-temperature melting, pour the melted raw material into a twin-screw extruder, and extrude it to prepare the bag holder;
[0029] Step 3: Seal and press the bag seat and the bag body to obtain a self-supporting compressed bag.
[0030] The film blowing temperature of the film blowing machine is 130°C.
Embodiment 1
[0032] A self-supporting compression bag, comprising a bag body and a bag seat, the bag body is measured in parts by weight, including: the bag body is measured in parts by weight, including: 46 parts of ethylene, 13 parts of polytetrafluoroethylene, 14 parts of kaolin, and cryolite 9 parts, 4 parts of lubricant, 2 parts of stabilizer and 2 parts of plasticizer; the bag seat is calculated by weight, including: 16 parts of polyether polyurethane, 7 parts of tree ash, 12 parts of ethylene propylene rubber, high carbon chromium 7 parts of iron powder, 3 parts of nano titanium dioxide, 4 parts of polyethylene wax micropowder, 7 parts of titanium dioxide, 4 parts of tributyl phosphate, 5 parts of polyacrylamide and 11 parts of compatibilizer.
[0033] A preparation process for a self-supporting compression bag, comprising the steps of:
[0034] Step 1: Put the raw material of the bag body in the reaction kettle to melt at high temperature, and put the melted raw material into the f...
Embodiment 2
[0038] A self-supporting compression bag, comprising a bag body and a bag seat, the bag body is measured in parts by weight, including: the bag body is measured in parts by weight, including: 45 parts of ethylene, 12 parts of polytetrafluoroethylene, 13 parts of kaolin, and cryolite 8 parts, 3 parts of lubricant, 1 part of stabilizer and 1 part of plasticizer; the bag seat is calculated by weight, including: 15 parts of polyether polyurethane, 5 parts of tree ash, 10 parts of ethylene propylene rubber, high carbon chromium 5 parts of iron powder, 1 part of nano titanium dioxide, 1 part of polyethylene wax fine powder, 6 parts of titanium dioxide, 1 part of tributyl phosphate, 4 parts of polyacrylamide and 10 parts of compatibilizer.
[0039] A preparation process for a self-supporting compression bag, comprising the steps of:
[0040] Step 1: Put the raw material of the bag body in the reaction kettle to melt at high temperature, and put the melted raw material into the film b...
PUM
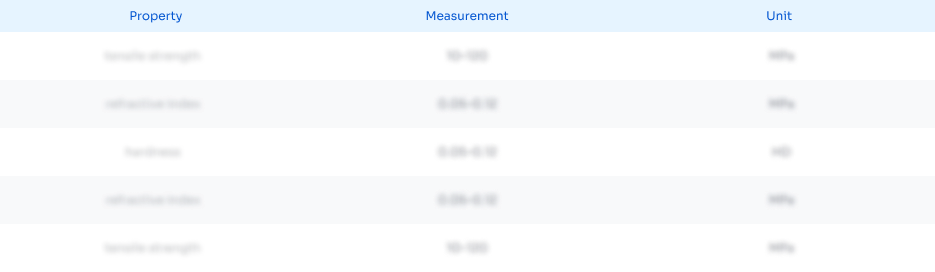
Abstract
Description
Claims
Application Information

- Generate Ideas
- Intellectual Property
- Life Sciences
- Materials
- Tech Scout
- Unparalleled Data Quality
- Higher Quality Content
- 60% Fewer Hallucinations
Browse by: Latest US Patents, China's latest patents, Technical Efficacy Thesaurus, Application Domain, Technology Topic, Popular Technical Reports.
© 2025 PatSnap. All rights reserved.Legal|Privacy policy|Modern Slavery Act Transparency Statement|Sitemap|About US| Contact US: help@patsnap.com