Machining method of wing-shaped missile shaft high-precision part
A processing method and high-precision technology, applied in the processing field of high-precision parts of airfoil elastic shaft, can solve problems such as deformation and distortion, inability to achieve real-time monitoring of the elastic wing, affecting the high-precision requirements of calibration instruments, etc. Effects of Balance Problems
- Summary
- Abstract
- Description
- Claims
- Application Information
AI Technical Summary
Problems solved by technology
Method used
Image
Examples
no. 1 approach
[0076] This embodiment relates to a method for processing high-precision parts of an airfoil shaft, comprising the following steps:
[0077] Step 001. Selecting raw materials for processing target airfoil parts and blanking;
[0078] Step 002. Split the target airfoil part into welding pieces according to the part structure, and obtain the raw materials required for each welding piece;
[0079] Step 003. Machining each welded single piece;
[0080] Step 004. Assemble and weld the single pieces to form the wing assembly, and vibrate to relieve stress;
[0081] Step 005. Take two wing assemblies, and use an auxiliary processing device to clamp the two wing assemblies at the same time. The two wing assemblies and the auxiliary processing device form a rotary structure, and the rotary structure can rotate around the center of rotation;
[0082] Step 006. Continue to machine the structure of the revolving body, remove the auxiliary processing device until it becomes the target ai...
no. 2 approach
[0092] This embodiment relates to a method for processing high-precision parts of an airfoil shaft, comprising the following steps:
[0093] Step 001. Selecting raw materials for processing target airfoil parts and blanking;
[0094] Step 002. Split the target airfoil part into welding pieces according to the part structure, and obtain the raw materials required for each welding piece;
[0095] Step 003. Machining each welded single piece;
[0096] Step 004. Assemble and weld the single pieces to form the wing assembly, and vibrate to relieve stress;
[0097] Step 005. Take two wing assemblies, and use an auxiliary processing device to clamp the two wing assemblies at the same time. The two wing assemblies and the auxiliary processing device form a rotary structure, and the rotary structure can rotate around the center of rotation;
[0098] Step 006. Continue to machine the structure of the revolving body, remove the auxiliary processing device until it becomes the target ai...
PUM
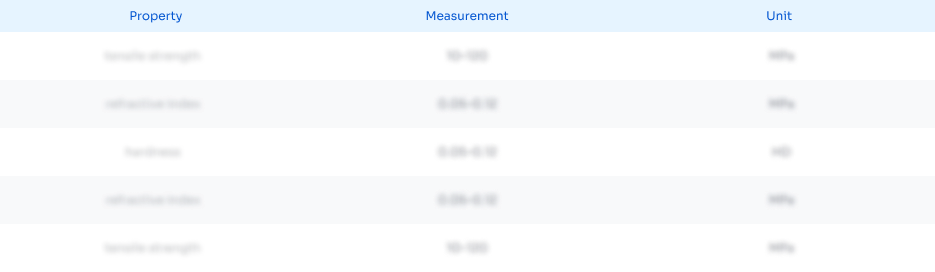
Abstract
Description
Claims
Application Information

- R&D
- Intellectual Property
- Life Sciences
- Materials
- Tech Scout
- Unparalleled Data Quality
- Higher Quality Content
- 60% Fewer Hallucinations
Browse by: Latest US Patents, China's latest patents, Technical Efficacy Thesaurus, Application Domain, Technology Topic, Popular Technical Reports.
© 2025 PatSnap. All rights reserved.Legal|Privacy policy|Modern Slavery Act Transparency Statement|Sitemap|About US| Contact US: help@patsnap.com