Heating method of hollow ingot
A heating method and hollow ingot technology, applied in the field of engineering applications, can solve problems such as inner surface oxidation, and achieve the effects of reducing extrusion defects, reducing inner surface oxidation problems, and low risk
- Summary
- Abstract
- Description
- Claims
- Application Information
AI Technical Summary
Problems solved by technology
Method used
Examples
Embodiment 1
[0019] Before heating:
[0020] Place the graphite rod in the hollow ingot; the stone mill rod is processed according to the length and inner diameter of the hollow ingot, the diameter of the stone mill rod is 8mm smaller than the inner diameter of the hollow ingot, and the length of the stone mill rod is the same as the length of the hollow ingot. Adjust the heating temperature (35°C higher than the extrusion temperature) and time to a suitable range. Place 8 hollow ingots with graphite rods in the copper ingot heating furnace. Before starting the furnace, place the hollow ingots with graphite rods at 150 mm from the exit end of the induction heating coil in the copper ingot heating furnace. Under the premise, it must not be advanced.
[0021] Heating process:
[0022] Observe continuously through the observation hole, pay special attention to the temperature of the billet during the heating process, and gradually increase the temperature to prevent local overheating and ma...
Embodiment 2
[0026] Before heating:
[0027] Place the graphite rod in the hollow ingot; the stone mill rod is processed according to the length and inner diameter of the hollow ingot, the diameter of the stone mill rod is 2mm smaller than the inner diameter of the hollow ingot, and the length of the stone mill rod is the same as the length of the hollow ingot. Adjust the heating temperature (55°C higher than the extrusion temperature) and time to an appropriate range. Place 4 hollow ingots with graphite rods in the copper ingot heating furnace. Before starting the furnace, place the hollow ingots with graphite rods at 250mm from the exit end of the induction heating coil in the copper ingot heating furnace. Under the premise, it must not be advanced.
[0028] Heating process:
[0029] Observe continuously through the observation hole, pay special attention to the temperature of the billet during the heating process, and gradually increase the temperature to prevent local overheating and...
PUM
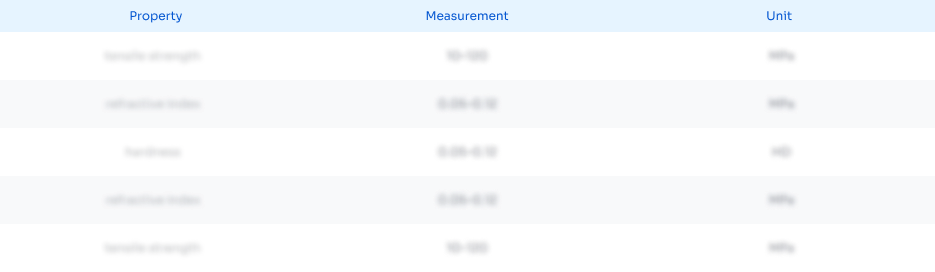
Abstract
Description
Claims
Application Information

- R&D
- Intellectual Property
- Life Sciences
- Materials
- Tech Scout
- Unparalleled Data Quality
- Higher Quality Content
- 60% Fewer Hallucinations
Browse by: Latest US Patents, China's latest patents, Technical Efficacy Thesaurus, Application Domain, Technology Topic, Popular Technical Reports.
© 2025 PatSnap. All rights reserved.Legal|Privacy policy|Modern Slavery Act Transparency Statement|Sitemap|About US| Contact US: help@patsnap.com