Extrusion forming equipment for PVC pipe production
A PVC pipe, extrusion molding technology, applied in the field of extrusion molding equipment for PVC pipe production, can solve the problems of corrugated PVC plastic pipe surface convex defects, etc., to achieve the effect of avoiding difficult removal
- Summary
- Abstract
- Description
- Claims
- Application Information
AI Technical Summary
Problems solved by technology
Method used
Image
Examples
Embodiment 1
[0026] For example figure 1 -example Figure 5 Shown:
[0027] The present invention provides an extrusion molding equipment for PVC pipe production, the structure of which includes a heating bucket 1, a machine body 2, a support 3, a forming head 4, and an extrusion tube 5. The heating bucket 1 is embedded in the extrusion tube 5. At the upper end position, the body 2 is welded to the support 3, the extrusion tube 5 is embedded and connected to the body 2, the forming head 4 and the extrusion tube 5 are an integrated structure; the forming head 4 includes an outer frame 41. The middle solid block 42 and the inner frame 43. The middle solid block 42 and the outer frame 41 are an integrated structure, and the inner frame 43 is embedded and fixed at the inner side of the outer frame 41.
[0028] Wherein, the inner frame 43 includes connecting plate a1, telescopic block a2, lower connecting plate a3, and elastic sheet a4, the telescopic block a2 fits with the bottom of the conn...
Embodiment 2
[0034] For example Figure 6 -example Figure 8 Shown:
[0035] Wherein, the central solid block 42 includes a shrinkage plate c1, a receiving plate c2, a rebound strip c3, and a front plate c4, the shrinkage plate c1 is movably engaged with the receiving plate c2, and the complex elastic strip c3 is installed on the receiving plate Between c2 and the contraction plate c1, the front plate c4 and the receiving plate c2 are of an integrated structure. The extrusion of the plastic to the shrink board c1 can make the shrink board c1 shrink inwardly.
[0036] Wherein, the front plate c4 includes a combination plate c41, an air guide cavity c42, and an overhanging block c43. Together, there are six stretching blocks c43, which are evenly distributed in parallel at the front end of the connecting plate c41, and the extruding airflow inside the object can push the stretching blocks c43 to protrude forward.
[0037] Wherein, the extension block c43 includes a plate d1, an extension p...
PUM
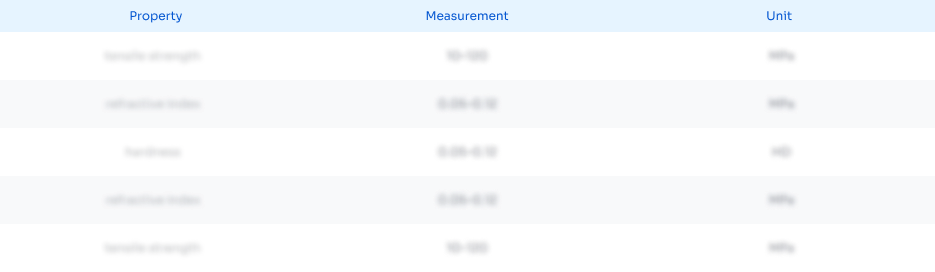
Abstract
Description
Claims
Application Information

- R&D Engineer
- R&D Manager
- IP Professional
- Industry Leading Data Capabilities
- Powerful AI technology
- Patent DNA Extraction
Browse by: Latest US Patents, China's latest patents, Technical Efficacy Thesaurus, Application Domain, Technology Topic, Popular Technical Reports.
© 2024 PatSnap. All rights reserved.Legal|Privacy policy|Modern Slavery Act Transparency Statement|Sitemap|About US| Contact US: help@patsnap.com