Trapezoidal wave back electromotive force brushless direct current motor commutation error compensation method
A technology of brushed DC motor and counter electromotive force, applied in the direction of electronic commutator, monitoring commutation, control purpose model/simulation, etc., to achieve the effect of reducing the number of times, optimizing the width of the hysteresis loop, and increasing the compensation speed
- Summary
- Abstract
- Description
- Claims
- Application Information
AI Technical Summary
Problems solved by technology
Method used
Image
Examples
Embodiment Construction
[0028] The technical solution of the present invention will be further described in detail below in conjunction with the accompanying drawings.
[0029] figure 1 It is a flow chart of the commutation error compensation method for the brushless DC motor of the trapezoidal wave back electromotive force of the present invention. From figure 1 It can be seen from the figure that the brushless DC motor commutation error compensation method of the present invention includes two steps. First, the initial estimated value of the commutation error is obtained based on the mathematical model of the brushless DC motor, and then online scrolling is performed based on the difference of the phase current integral. Optimize to obtain the best commutation error, and perform hysteresis control after the online rolling optimization ends. At the same time, according to the motor speed and load changes, the hysteresis band width is updated in real time to overcome the influence of uncertainty on...
PUM
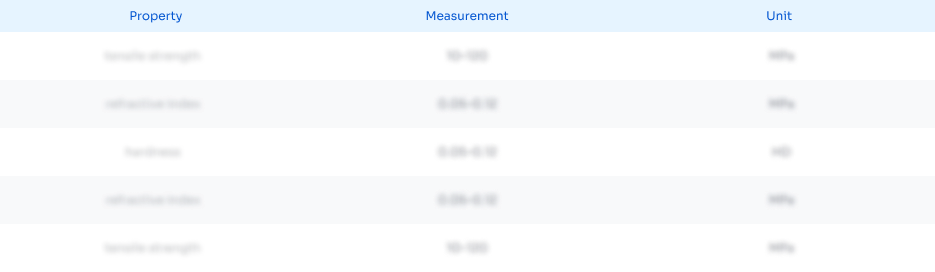
Abstract
Description
Claims
Application Information

- Generate Ideas
- Intellectual Property
- Life Sciences
- Materials
- Tech Scout
- Unparalleled Data Quality
- Higher Quality Content
- 60% Fewer Hallucinations
Browse by: Latest US Patents, China's latest patents, Technical Efficacy Thesaurus, Application Domain, Technology Topic, Popular Technical Reports.
© 2025 PatSnap. All rights reserved.Legal|Privacy policy|Modern Slavery Act Transparency Statement|Sitemap|About US| Contact US: help@patsnap.com