Repair method for interfacial delamination defect of filament wound engine casing
A technology for engine casings and delamination defects, which is used in climate sustainability, sustainable transportation, air transportation, etc., can solve problems affecting the strength of composite layers, casing shape and position tolerances, etc., and achieve the effect of improving quality reliability.
- Summary
- Abstract
- Description
- Claims
- Application Information
AI Technical Summary
Problems solved by technology
Method used
Image
Examples
Embodiment Construction
[0087] The present invention will be further described in detail below with reference to the accompanying drawings and specific embodiments.
[0088] The repair method for interfacial delamination defect of filament wound engine casing is especially suitable for debonding repair of the position where the thermal insulation layer is more than 10mm. The delamination defect repair of interface includes defect identification, defect removal, composite layer reset, cold bonding repair and hot bonding repair. Specific steps are as follows:
[0089] 1) First ultrasonic inspection and then DR inspection to accurately locate the position of the interface delamination defect, and draw the defect edge identification line on the surface of the thermal insulation layer
[0090] In order to accurately define the defect position, during the ultrasonic inspection process, the defects of plastic mold cloth are pasted on the edge of the interface delamination defect, which is used as a referenc...
PUM
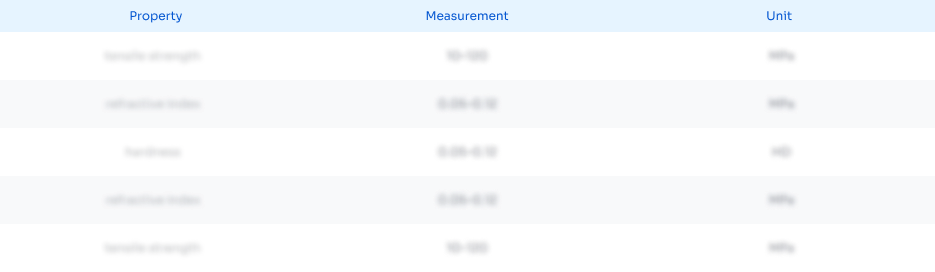
Abstract
Description
Claims
Application Information

- R&D
- Intellectual Property
- Life Sciences
- Materials
- Tech Scout
- Unparalleled Data Quality
- Higher Quality Content
- 60% Fewer Hallucinations
Browse by: Latest US Patents, China's latest patents, Technical Efficacy Thesaurus, Application Domain, Technology Topic, Popular Technical Reports.
© 2025 PatSnap. All rights reserved.Legal|Privacy policy|Modern Slavery Act Transparency Statement|Sitemap|About US| Contact US: help@patsnap.com