A multi-level structure microchannel mixer and its fluid mixing method
A microchannel and mixer technology, applied in fluid mixers, chemical instruments and methods, mixers, etc., can solve problems such as easy clogging, installation and cleaning, difficult process control, complex flow patterns, etc., and achieve good mixing effect and intensified Fluid disturbance, the effect of increasing the fluid flow velocity
- Summary
- Abstract
- Description
- Claims
- Application Information
AI Technical Summary
Problems solved by technology
Method used
Image
Examples
Embodiment 1
[0084] The microchannel mixer in the present embodiment comprises two stages of fluid distribution channels ( figure 1 ), the entrance channel is 500 μm wide, 500 μm deep, and 30 mm long. The width of the first-stage fluid distribution channel is 800 μm, the depth is 500 μm, and the length is 40 mm. The angle α between the inlet channel and the first-stage fluid distribution channel is 90°. The second-stage fluid distribution channel has a width of 500 μm, a depth of 300 μm, and a length of 15 mm. The angle β between the branch channel of the first-stage fluid distribution channel and the second-stage fluid distribution channel is 90°. The width of all process fluid channels is 250 μm, the depth is 250 μm, the length is 15 mm, and the width of the tapered outlet is 150 μm ( figure 2 ). The angle γ formed between the two process fluid channels and the branch channel of the second-stage fluid distribution channel connected together is 120°. The width of the fluid impingeme...
Embodiment 2
[0096] The microchannel mixer used in this embodiment comprises three stages of fluid distribution channels ( image 3 ), the third-stage fluid distribution channel has a width of 300 μm, a depth of 210 μm, and a length of 7 mm. The angle β between the branch channel of the second-stage fluid distribution channel and the third-stage fluid distribution channel is 90°. All other structural parameters of the microchannel mixer and the microscopic mixing measurement method are the same as in Example 1. The separation factor measured in this example is 0.0021, and the total pressure drop at the inlet and outlet is 117Pa.
Embodiment 3
[0098] The microchannel mixer used in this embodiment includes four stages of fluid distribution channels, the width of the fourth stage fluid distribution channel is 200 μm, the depth is 150 μm, and the length is 4 mm. The angle β between the branch channel of the third-stage fluid distribution channel and the fourth-stage fluid distribution channel is 90°. All other structural parameters of the microchannel mixer and the microscopic mixing measurement method are the same as in Example 2, the measured separation factor is 0.0018, and the total pressure drop at the inlet and outlet is 125Pa.
[0099] The comparison of Examples 1, 2 and 3 shows that increasing the number of stages of fluid distribution channels is conducive to enhancing the mixing effect.
PUM
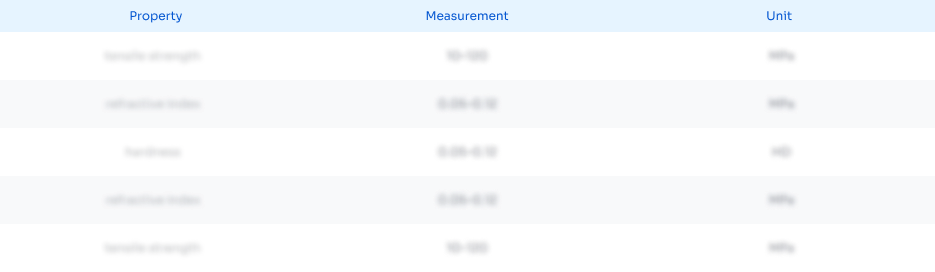
Abstract
Description
Claims
Application Information

- R&D
- Intellectual Property
- Life Sciences
- Materials
- Tech Scout
- Unparalleled Data Quality
- Higher Quality Content
- 60% Fewer Hallucinations
Browse by: Latest US Patents, China's latest patents, Technical Efficacy Thesaurus, Application Domain, Technology Topic, Popular Technical Reports.
© 2025 PatSnap. All rights reserved.Legal|Privacy policy|Modern Slavery Act Transparency Statement|Sitemap|About US| Contact US: help@patsnap.com