Preparation method of water-based flexographic printing ink
A flexographic and ink technology, applied in the field of preparation of water-based flexographic inks, can solve the problems of inhibiting rapid development and application, poor scratch resistance and wear resistance, single applicable substrate, etc., and achieves good storage stability, not easy to blur, The effect of low production cost
- Summary
- Abstract
- Description
- Claims
- Application Information
AI Technical Summary
Problems solved by technology
Method used
Image
Examples
Embodiment 1
[0022] A preparation method of water-based flexographic printing ink, comprises the steps:
[0023] (1) Take the raw materials according to parts by weight: 55 parts of water-soluble acrylic resin, 45 parts of water-based pigment, 2 parts of ethanol, 0.5 part of polydimethylsiloxane, 1 part of sodium lignosulfonate, CW-0601 defoaming 0.3 parts of antibacterial agent linoleum oil, 0.5 parts of wax emulsion; 2 parts of triethanolamine buffer with a pH value of 8.5 to 9.0, 3 parts of sodium alginate and 50 parts of water, set aside;
[0024] (2) Add water to the reaction kettle first, control the temperature of the reaction kettle between 90°C, then slowly add water-soluble acrylic resin, ethanol and CW-0601 defoamer in turn under stirring conditions, keep warm for 40 minutes, mix Stir well to form a base material;
[0025] (3) Reduce the temperature of the reactor to 35°C-40°C, add triethanolamine buffer to the base material in step (2), and adjust the pH value of the base mate...
Embodiment 2
[0028] A preparation method of water-based flexographic printing ink, comprises the steps:
[0029] (1) Raw materials by weight: 60 parts of water-soluble acrylic resin, 47 parts of water-based pigment, 3 parts of ethanol, 0.9 part of polydimethylsiloxane, 1.2 parts of sodium lignosulfonate, CW-0601 defoaming 0.4 parts of antibacterial agent Zanthoxylum volatile oil, 0.7 parts of wax emulsion; 2.5 parts of triethanolamine buffer with a pH value of 8.5 to 9.0, 4 parts of sodium alginate and 55 parts of water, set aside;
[0030] (2) Add water to the reaction kettle first, control the temperature of the reaction kettle between 80°C and 90°C, then slowly add water-soluble acrylic resin, ethanol and CW-0601 defoamer under stirring conditions, and keep warm for 45 Minutes, mix and stir evenly to form a bottom material;
[0031] (3) Reduce the temperature of the reactor to 35°C-40°C, add triethanolamine buffer to the base material in step (2), and adjust the pH value of the base ma...
Embodiment 3
[0034] A preparation method of water-based flexographic printing ink, comprises the steps:
[0035] (1) Raw materials by weight: 62 parts of water-soluble acrylic resin, 48 parts of water-based pigment, 3.5 parts of ethanol, 1.0 part of polydimethylsiloxane, 1.3 parts of sodium lignosulfonate, CW-0601 defoaming 0.4 parts of antibacterial agent linoleum oil, 0.8 parts of wax emulsion; 2.8 parts of triethanolamine buffer with a pH value of 8.5 to 9.0, 4.5 parts of sodium alginate and 58 parts of water, set aside;
[0036] (2) Add water to the reaction kettle first, control the temperature of the reaction kettle between 80°C and 90°C, then slowly add water-soluble acrylic resin, ethanol and CW-0601 defoamer under stirring conditions, and keep warm for 48 Minutes, mix and stir evenly to form a bottom material;
[0037] (3) Reduce the temperature of the reactor to 35°C-40°C, add triethanolamine buffer to the base material in step (2), and adjust the pH value of the base material t...
PUM
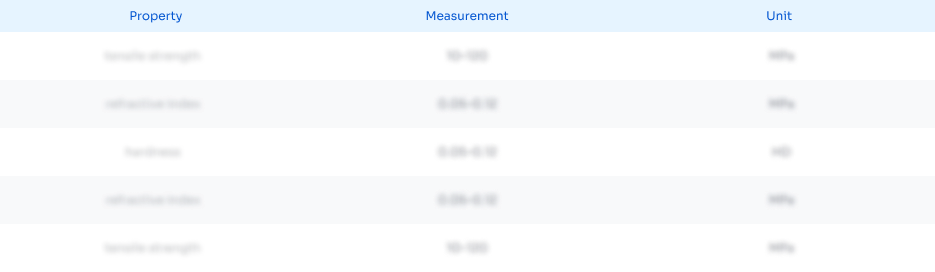
Abstract
Description
Claims
Application Information

- R&D Engineer
- R&D Manager
- IP Professional
- Industry Leading Data Capabilities
- Powerful AI technology
- Patent DNA Extraction
Browse by: Latest US Patents, China's latest patents, Technical Efficacy Thesaurus, Application Domain, Technology Topic, Popular Technical Reports.
© 2024 PatSnap. All rights reserved.Legal|Privacy policy|Modern Slavery Act Transparency Statement|Sitemap|About US| Contact US: help@patsnap.com