Oil tank fluid-solid coupling transient analysis method and system considering liquid additional mass
An additional mass, transient analysis technology, applied in instrumentation, geometric CAD, design optimization/simulation, etc., can solve problems such as inaccurate displacement transmitted to the fluid domain, inaccurate structural deformation, and inconsistency between dynamic stress and dynamic response. Accurate response, real and reliable force
- Summary
- Abstract
- Description
- Claims
- Application Information
AI Technical Summary
Problems solved by technology
Method used
Image
Examples
Embodiment Construction
[0028] The embodiment of the present invention provides a fluid-solid coupling transient analysis method of the fuel tank considering the additional mass of the liquid, which considers the influence of the additional mass generated by the dynamic pressure of the liquid on the surface of the structure, and considers the dynamic characteristics of the structure when calculating the stress. The real-time coupling between the liquid and the solid in the fuel tank transmits the force of the liquid to the structure from time to time. The force of the structure is more real and reliable, the response is more accurate, and it is closer to the actual situation. It can accurately simulate the structural fatigue of the fuel tank caused by the sloshing of the liquid. Correspondingly, the embodiment of the present invention also provides a fluid-solid coupling transient analysis system of the fuel tank considering the additional mass of the liquid.
[0029] The present invention will be des...
PUM
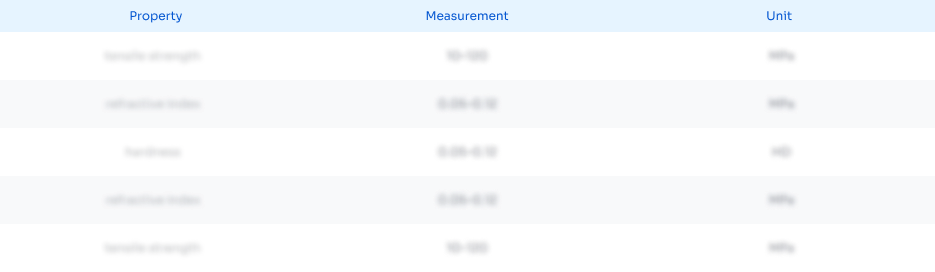
Abstract
Description
Claims
Application Information

- R&D Engineer
- R&D Manager
- IP Professional
- Industry Leading Data Capabilities
- Powerful AI technology
- Patent DNA Extraction
Browse by: Latest US Patents, China's latest patents, Technical Efficacy Thesaurus, Application Domain, Technology Topic, Popular Technical Reports.
© 2024 PatSnap. All rights reserved.Legal|Privacy policy|Modern Slavery Act Transparency Statement|Sitemap|About US| Contact US: help@patsnap.com