Millimeter-wave radar and camera rapid joint calibration method
A millimeter-wave radar and joint calibration technology, applied in image analysis, image data processing, radio wave measurement systems, etc., can solve the problems of reduced calibration accuracy, poor reflection intensity, irregular shape, etc., to improve joint calibration speed, reflection strong effect
- Summary
- Abstract
- Description
- Claims
- Application Information
AI Technical Summary
Problems solved by technology
Method used
Image
Examples
Embodiment 1
[0050] Such as figure 1 As shown, a rapid joint calibration method of millimeter-wave radar and camera 2 includes the following steps:
[0051] S1. Install the millimeter-wave radar and camera 2 to the fixed position of the motion platform 1, that is, the position of the front of the vehicle, and place the motion platform 1 in an open and flat place, which can be an outdoor square or an indoor flat hall;
[0052] S2. Place the corner reflector 4 directly in front of the millimeter-wave radar so that it faces the front of the vehicle, adjust its height so that the reflector is roughly the same height as the millimeter-wave radar, and adjust the distance of the reflector so that it can appear in the image of the camera 2;
[0053] S3. Use the pinhole camera model to calibrate the internal parameters of the binocular camera 2. In general applications, the measurement data of the millimeter-wave radar only needs to be projected onto one image plane. In this embodiment, the left ob...
PUM
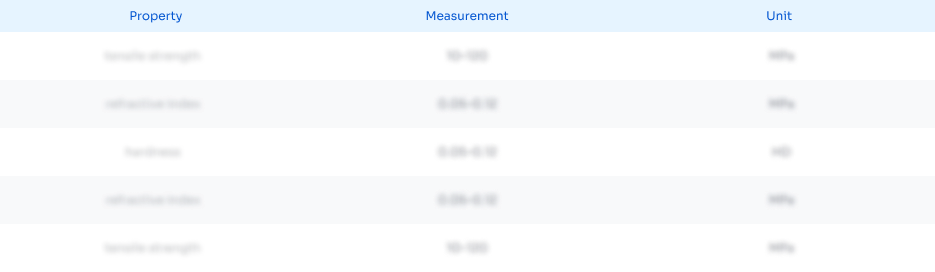
Abstract
Description
Claims
Application Information

- Generate Ideas
- Intellectual Property
- Life Sciences
- Materials
- Tech Scout
- Unparalleled Data Quality
- Higher Quality Content
- 60% Fewer Hallucinations
Browse by: Latest US Patents, China's latest patents, Technical Efficacy Thesaurus, Application Domain, Technology Topic, Popular Technical Reports.
© 2025 PatSnap. All rights reserved.Legal|Privacy policy|Modern Slavery Act Transparency Statement|Sitemap|About US| Contact US: help@patsnap.com