Melt-blow molding process of fiber pillow
A technology of melt-blown molding and fiber, which is applied in the direction of pillows, textiles, papermaking, non-woven fabrics, etc., which can solve the problems of unfavorable fiber pillow cleaning and long-term use, fiber pillows that cannot be washed, easy to clump, and broken cotton, etc.
- Summary
- Abstract
- Description
- Claims
- Application Information
AI Technical Summary
Problems solved by technology
Method used
Examples
Embodiment 1
[0013] A melt-blown molding process for fiber pillows, comprising the following steps:
[0014] (1) Select raw materials: mix the raw material fibers as required, loosen and stir to process them into uniformly mixed short fibers;
[0015] (2) the homogeneously mixed short fibers obtained in step (1) are evenly fed to the carding machine through the feeder, and combed into a fluffy fiber mixture with a certain thickness;
[0016] (3) feeding the fluffy fiber mixture that step (2) obtains to the hopper for stock preparation and secondary stirring, waiting for cotton spraying;
[0017] (4) After stabilizing the air compressed by the air compressor to an air pressure of 6, connect the air compressor to the air storage tank, compress the air to the heating tank through the air storage tank, and then heat the air to 120°C by the heating tank to spray cotton;
[0018] (5) The prepared mixed fiber cotton will produce honeycomb coagulation after spraying cotton under high temperature...
Embodiment 2
[0022] A melt-blown molding process for fiber pillows, comprising the following steps:
[0023] (1) Select raw materials: mix the raw material fibers as required, loosen and stir to process them into uniformly mixed short fibers;
[0024] (2) the homogeneously mixed short fibers obtained in step (1) are evenly fed to the carding machine through the feeder, and combed into a fluffy fiber mixture with a certain thickness;
[0025] (3) feeding the fluffy fiber mixture that step (2) obtains to the hopper for stock preparation and secondary stirring, waiting for cotton spraying;
[0026] (4) After stabilizing the air compressed by the air compressor to the air pressure of 8, connect the air compressor to the air storage tank, compress the air to the heating tank through the air storage tank, and then heat the air to 120-250 Spray cotton after ℃;
[0027] (5) The prepared mixed fiber cotton will produce honeycomb coagulation after spraying cotton under high temperature and high pr...
Embodiment 3
[0031] A melt-blown molding process for fiber pillows, comprising the following steps:
[0032] (1) Select raw materials: mix the raw material fibers as required, loosen and stir to process them into uniformly mixed short fibers;
[0033] (2) the homogeneously mixed short fibers obtained in step (1) are evenly fed to the carding machine through the feeder, and combed into a fluffy fiber mixture with a certain thickness;
[0034] (3) feeding the fluffy fiber mixture that step (2) obtains to the hopper for stock preparation and secondary stirring, waiting for cotton spraying;
[0035] (4) After stabilizing the air compressed by the air compressor to an air pressure of 7, connect the air compressor to the air storage tank, compress the air to the heating tank through the air storage tank, and then heat the air to 200°C by the heating tank to spray cotton;
[0036] (5) The prepared mixed fiber cotton will produce honeycomb coagulation after spraying cotton under high temperature...
PUM
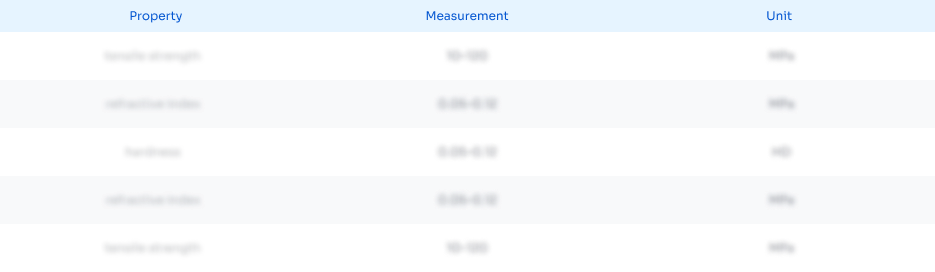
Abstract
Description
Claims
Application Information

- Generate Ideas
- Intellectual Property
- Life Sciences
- Materials
- Tech Scout
- Unparalleled Data Quality
- Higher Quality Content
- 60% Fewer Hallucinations
Browse by: Latest US Patents, China's latest patents, Technical Efficacy Thesaurus, Application Domain, Technology Topic, Popular Technical Reports.
© 2025 PatSnap. All rights reserved.Legal|Privacy policy|Modern Slavery Act Transparency Statement|Sitemap|About US| Contact US: help@patsnap.com