Improved galvanization process of power pole
A power pole and process technology, applied in the field of galvanizing process of power poles, can solve the problems of unreasonable matching of process parameters, high operator experience requirements, unreasonable process settings, etc., so as to avoid over-pickling and improve labor. environment, the effect of improving the resistance to atmospheric corrosion
- Summary
- Abstract
- Description
- Claims
- Application Information
AI Technical Summary
Problems solved by technology
Method used
Examples
Embodiment 1
[0019] An improved galvanizing process for power poles according to the present invention is characterized in that it comprises the following steps,
[0020] (1) Pickling and phosphating the power pole;
[0021] (2) Burn the power pole;
[0022] (3) Grinding the power pole;
[0023] (4) Dip the power rod in the plating aid, put the power rod into the pressure vacuum tank, the vacuum pressure is 0.45Mpa, then suck the dipping aid in negative pressure, the dipping aid is 12mm higher than the product, continue vacuuming for 35 minutes, Then slowly release the pressure to normal pressure, then soak for 8 minutes, then take out the product and put it on a drier to shake off the dipping flux, wherein the dipping flux adopts 19% ammonium chloride, 2.8% zinc chloride, 2.5% sodium bicarbonate mixed liquid, keep the temperature at 68°C for 8 minutes;
[0024] (5) The electric rod is hot-dip galvanized, and the temperature of the zinc bath, the dipping time and the speed at which the ...
Embodiment 2
[0032] An improved galvanizing process for power poles according to the present invention is characterized in that it comprises the following steps,
[0033] (1) Pickling and phosphating the power pole;
[0034] (2) Burn the power pole;
[0035] (3) Grinding the power pole;
[0036] (4) Dip the power rod in the plating aid, put the power rod into the pressure vacuum tank, the vacuum pressure is 0.55Mpa, then suck the dipping aid in negative pressure, the dipping aid is 16mm higher than the product, continue to vacuum for 42 minutes, Then slowly release the pressure to normal pressure, then soak for 8 minutes, then take out the product and put it on a drier to shake off the dipping flux, wherein the dipping flux adopts 21% ammonium chloride, 3.1% zinc chloride, 3.4% sodium bicarbonate mixed liquid, keep the temperature at 72°C for 6 minutes;
[0037] (5) Hot-dip galvanizing for the electric rod, and control the temperature of the zinc bath, the dipping time and the speed at ...
PUM
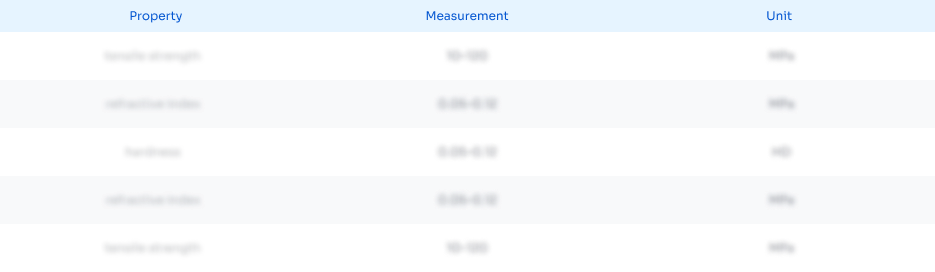
Abstract
Description
Claims
Application Information

- R&D
- Intellectual Property
- Life Sciences
- Materials
- Tech Scout
- Unparalleled Data Quality
- Higher Quality Content
- 60% Fewer Hallucinations
Browse by: Latest US Patents, China's latest patents, Technical Efficacy Thesaurus, Application Domain, Technology Topic, Popular Technical Reports.
© 2025 PatSnap. All rights reserved.Legal|Privacy policy|Modern Slavery Act Transparency Statement|Sitemap|About US| Contact US: help@patsnap.com