Automatic displacement compensation thrust bearing
A displacement compensation and thrust bearing technology, applied in the field of thrust bearings, can solve the problems of reduced sealing performance, low propulsion efficiency, and excessive compression of the end face sealing surface.
- Summary
- Abstract
- Description
- Claims
- Application Information
AI Technical Summary
Problems solved by technology
Method used
Image
Examples
Embodiment Construction
[0021] like figure 1 , figure 2 In the automatic displacement compensation thrust bearing shown, a convex disc-shaped thrust disc 12 is arranged on the thrust shaft 2, and the thrust shaft 2 and the thrust disc 12 are connected as one; Coupling 1 is a rigid coupling. The left end plate 10 and the right end plate 4 are rotatably supported on the thrust shaft 2 on the left and right sides of the thrust plate 12 through rolling bearings. Located on the center line of the bearing housing 7 , the left end plate 10 and the right end plate 4 , seals are provided on the mounting surfaces of the left end plate 10 , the right end plate 4 and the two ends of the bearing housing 7 .
[0022] A displacement compensation piston 5 is slidably arranged in the bearing housing 7. The center position of the displacement compensation piston 5 has a central through hole. The outer surface of the displacement compensation piston 5 is a cylindrical surface, and a sealing ring is arranged on the c...
PUM
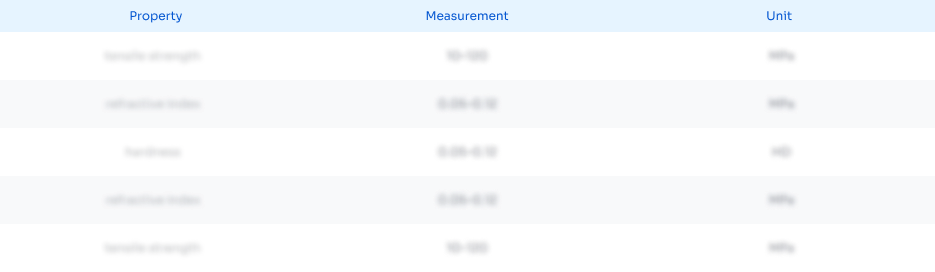
Abstract
Description
Claims
Application Information

- Generate Ideas
- Intellectual Property
- Life Sciences
- Materials
- Tech Scout
- Unparalleled Data Quality
- Higher Quality Content
- 60% Fewer Hallucinations
Browse by: Latest US Patents, China's latest patents, Technical Efficacy Thesaurus, Application Domain, Technology Topic, Popular Technical Reports.
© 2025 PatSnap. All rights reserved.Legal|Privacy policy|Modern Slavery Act Transparency Statement|Sitemap|About US| Contact US: help@patsnap.com