Pyrolysis method of polyolefin waste plastic
A technology for waste plastics and polyolefins, which is applied in the field of resource utilization of waste plastics, can solve the problems of unfavorable large-scale commercial utilization, deactivation of molecular sieve catalysts, and high economic costs, and achieves improved catalytic activity and target product selectivity. The effect of low cost and long catalytic life
- Summary
- Abstract
- Description
- Claims
- Application Information
AI Technical Summary
Problems solved by technology
Method used
Examples
Embodiment 1
[0019] The catalyst used was obtained by the following modification method: the activated carbon catalyst was immersed in a 5mol / L nitric acid solution, stirred at 90°C for 6 hours, the impregnated activated carbon was filtered and washed with deionized water until neutral, and the filter material was Put it into a blast drying oven at 90°C and dry to constant weight to obtain nitric acid-modified activated carbon.
[0020] Using the above-mentioned modified activated carbon to catalyze the pyrolysis of low-density polyethylene, put the prepared modified activated carbon and polyolefin waste plastics in a fixed-bed reactor at a mass ratio of 2:1, and rapidly raise the temperature to 500 °C under the protection of an inert atmosphere. Perform online catalytic pyrolysis at ℃ for 20 minutes, and then quickly condense the products generated by catalytic pyrolysis to obtain liquid products, use air bags to collect non-condensable gases to obtain gas products, and the rest are solid ...
Embodiment 2
[0023] The catalyst used was obtained by the following modification method: soak the activated carbon catalyst in a 5mol / L nitric acid solution, stir at 60°C for 9 hours, filter the impregnated activated carbon, and wash it with deionized water until it is neutral. Put it into a blast drying oven at 90°C and dry to constant weight to obtain nitric acid-modified activated carbon.
[0024] Using the above-mentioned modified activated carbon to catalyze the pyrolysis of low-density polyethylene, put the prepared modified activated carbon and polyolefin waste plastics in a fixed-bed reactor at a mass ratio of 2:1, and rapidly raise the temperature to 500 °C under the protection of an inert atmosphere. Perform online catalytic pyrolysis at ℃ for 20 minutes, and then quickly condense the products generated by catalytic pyrolysis to obtain liquid products, use air bags to collect non-condensable gases to obtain gas products, and the rest are solid products.
[0025] The mass of liqui...
Embodiment 3
[0027] The catalyst used is obtained by the following modification method: impregnate the activated carbon catalyst in a 2mol / L nitric acid solution, stir at 90°C for 9 hours, filter the impregnated activated carbon, and wash it with deionized water until it is neutral. Put it into a blast drying oven at 90°C and dry to constant weight to obtain nitric acid-modified activated carbon.
[0028] Using the above-mentioned modified activated carbon to catalyze the pyrolysis of low-density polyethylene, put the prepared modified activated carbon and polyolefin waste plastics in a fixed-bed reactor at a mass ratio of 2:1, and rapidly raise the temperature to 500 °C under the protection of an inert atmosphere. Perform online catalytic pyrolysis at ℃ for 20 minutes, and then quickly condense the products generated by catalytic pyrolysis to obtain liquid products, use air bags to collect non-condensable gases to obtain gas products, and the rest are solid products.
[0029] The mass of ...
PUM
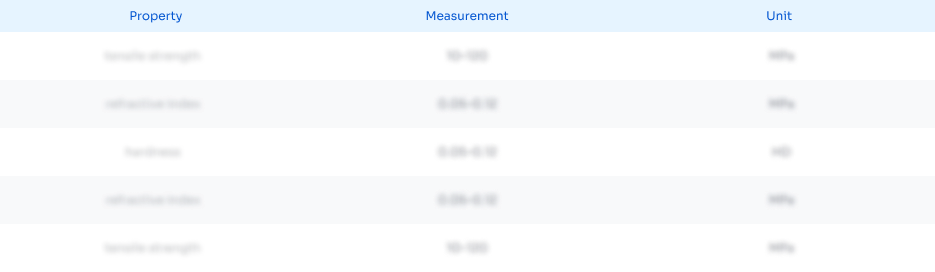
Abstract
Description
Claims
Application Information

- R&D Engineer
- R&D Manager
- IP Professional
- Industry Leading Data Capabilities
- Powerful AI technology
- Patent DNA Extraction
Browse by: Latest US Patents, China's latest patents, Technical Efficacy Thesaurus, Application Domain, Technology Topic, Popular Technical Reports.
© 2024 PatSnap. All rights reserved.Legal|Privacy policy|Modern Slavery Act Transparency Statement|Sitemap|About US| Contact US: help@patsnap.com