A method and system for forming parts based on additive manufacturing and hot isostatic pressing
A technology of additive manufacturing and hot isostatic pressing, which is applied in the fields of instrumentation, geometric CAD, design optimization/simulation, etc., can solve problems such as uneven stress distribution, achieve high preparation flexibility, reduce stress concentration, and overcome manufacturing difficulties Effect
- Summary
- Abstract
- Description
- Claims
- Application Information
AI Technical Summary
Problems solved by technology
Method used
Image
Examples
Embodiment 1
[0059] The structural shape of the part to be formed is such as figure 2 and image 3 As shown, its material is SUS316L.
[0060] First, according to the method in step S1, simulation simulation and structural stress analysis of the part to be formed are carried out, so as to obtain the area with large stress during the additive manufacturing process.
[0061] Then, the method in step S2 is used to redesign and optimize the area with high stress. In the embodiment of the present disclosure, the area is divided into discrete unit blocks to reduce the stress in the additive manufacturing process. Figure 4 where a and b are discrete unit blocks of different sizes, wherein the stress corresponding to the smaller size unit block is greater than that of the larger size unit block. Figure 4 The c in it is the dense shell conforming to the hot isostatic pressing process. Figure 4 The d in it is the exhaust port that conforms to the hot isostatic pressing process.
[0062] Next...
Embodiment 2
[0067] The structural shape of the part to be formed is such as figure 2 and image 3 As shown, its material is Ti6Al4V.
[0068] First, simulate and analyze the structural stress of the part to be formed according to the corresponding method in step S1, and obtain the area with large stress during the additive manufacturing process.
[0069] Then, the method in step S2 is used to redesign and optimize the area with high stress. In the embodiment of the present disclosure, the area is divided into a grid structure to reduce the stress in the additive manufacturing process. Figure 7 The e area in is the divided grid structure, Figure 8 It is an enlarged view of the grid structure, and each grid structure is connected with holes, so that each grid structure is connected to others. Figure 7 The f region in is a dense shell conforming to the hot isostatic pressing process, Figure 7 The g area in is the exhaust port that conforms to the hot isostatic pressing process.
[...
Embodiment 3
[0075] The structural shape of the part to be formed is such as figure 2 and image 3 As shown, its material is IN718.
[0076] First, simulate and analyze the structural stress of the part to be formed according to the corresponding method in step S1, and obtain the area with large stress during the additive manufacturing process.
[0077] Then, the method in step S2 is used to redesign and optimize the area with high stress. In the embodiment of the present disclosure, the area is divided into discrete unit blocks and grid structures to reduce the stress in the additive manufacturing process. Figure 11 The unit blocks of different structures are divided in the h region. Figure 11 The i region in the middle is the divided grid structure. Figure 11 The j in it is a dense shell conforming to the hot isostatic pressing process, which acts as a sheath for subsequent hot isostatic pressing. Figure 12 and Figure 13 It is part of the casings and parts manufactured by othe...
PUM
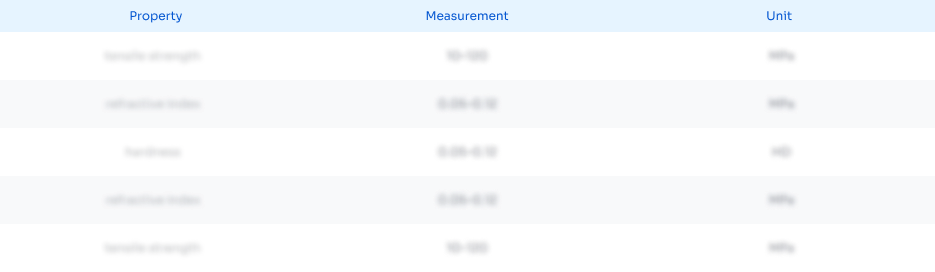
Abstract
Description
Claims
Application Information

- R&D
- Intellectual Property
- Life Sciences
- Materials
- Tech Scout
- Unparalleled Data Quality
- Higher Quality Content
- 60% Fewer Hallucinations
Browse by: Latest US Patents, China's latest patents, Technical Efficacy Thesaurus, Application Domain, Technology Topic, Popular Technical Reports.
© 2025 PatSnap. All rights reserved.Legal|Privacy policy|Modern Slavery Act Transparency Statement|Sitemap|About US| Contact US: help@patsnap.com