Composite pipe threaded joint
A technology of threaded joints and composite pipes, which is used in drill pipes, casings, drilling equipment, etc., can solve the problem that the sealing performance cannot meet the needs of use, and achieve the effect of preventing corrosion failure and high sealing performance.
- Summary
- Abstract
- Description
- Claims
- Application Information
AI Technical Summary
Problems solved by technology
Method used
Image
Examples
Embodiment Construction
[0021] Specific embodiments of the present invention will be described in detail below with reference to the accompanying drawings.
[0022] Such as Figure 1~5 As shown, the composite pipe threaded joint of the present invention includes a pipe body joint with external threads and a collar joint 5 with internal threads. The pipe body joint includes a pipe body 1 and an inner liner 2 fixed on the inner wall of the pipe body . The pipe body 1 is made of carbon steel, and the lining 2 is made of corrosion-resistant alloy. The purpose of adopting the composite pipe is to reduce the material cost of the pipe, the thickness of the inner lining 2 is 0.5-3 mm, and the pipe body 1 and the inner lining 2 are fixedly connected into one body.
[0023] The pipe body joint has a first threaded section 3, a first transition section 41, a first outer sealing surface section 42, a first shoulder 43 and a first inner sealing surface section 44 arranged in sequence; The second threaded secti...
PUM
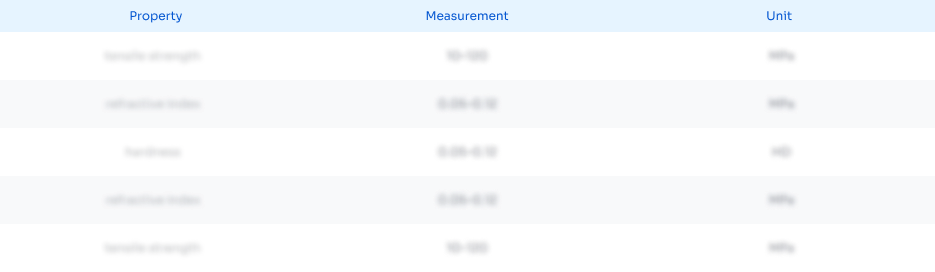
Abstract
Description
Claims
Application Information

- R&D
- Intellectual Property
- Life Sciences
- Materials
- Tech Scout
- Unparalleled Data Quality
- Higher Quality Content
- 60% Fewer Hallucinations
Browse by: Latest US Patents, China's latest patents, Technical Efficacy Thesaurus, Application Domain, Technology Topic, Popular Technical Reports.
© 2025 PatSnap. All rights reserved.Legal|Privacy policy|Modern Slavery Act Transparency Statement|Sitemap|About US| Contact US: help@patsnap.com