Production method of bamboo-wood fiber door plate
A technology of bamboo and wood fiber and production method, which is applied in the field of door panel processing, can solve the problems of limited use environment, complicated maintenance, and perishable door panels, so as to save later repair and maintenance costs, save wood consumption, and eliminate insects The effect of harassment
- Summary
- Abstract
- Description
- Claims
- Application Information
AI Technical Summary
Problems solved by technology
Method used
Examples
Embodiment 1
[0025] A kind of production method of bamboo wood fiber door panel, the steps are as follows:
[0026] 1) Weigh 15 parts of polyvinyl chloride resin, 11 parts of calcium carbonate and 26 parts of bamboo and wood by weight;
[0027] 2) Add calcium carbonate to the ball mill for ball mill dispersion treatment for 2 hours, and filter through a 10-mesh sieve to obtain calcium carbonate powder;
[0028] 3) The bamboo wood is cut into 3mm chopped fibers by a chopping machine, and filtered through a 10-mesh screen; bamboo wood powder is obtained;
[0029] 4) Add polyvinyl chloride resin, calcium carbonate powder and bamboo wood powder to a 120r / min mixer and knead for 30 minutes to obtain a mixed material. The working temperature of the mixer is 150°C;
[0030] 5) Transfer the mixed material obtained in step 4) to a twin-screw extruder with a host speed of 20r / pm for shearing and extrusion, and after water cooling and molding of the sizing die, the door panel base material is formed...
Embodiment 2
[0034] A kind of production method of bamboo wood fiber door panel, the steps are as follows:
[0035] 1) Weigh 20 parts of polyvinyl chloride resin, 17 parts of calcium carbonate and 32 parts of bamboo wood by weight;
[0036] 2) Add calcium carbonate to the ball mill for ball mill dispersion treatment for 2 hours, and filter through a 10-mesh sieve to obtain calcium carbonate powder;
[0037] 3) The bamboo wood is cut into 3mm chopped fibers by a chopping machine, and filtered through a 10-mesh screen; bamboo wood powder is obtained;
[0038] 4) Add polyvinyl chloride resin, calcium carbonate powder and bamboo wood powder to a 100r / min mixer and knead for 40 minutes to obtain a mixed material. The working temperature of the mixer is 250°C;
[0039] 5) Transfer the mixed material obtained in step 4) to a twin-screw extruder with a host speed of 30r / pm for shearing, extrusion, and water-cooling of the sizing die to form the door panel base material;
[0040] 6) After the doo...
Embodiment 3
[0043] A kind of production method of bamboo wood fiber door panel, the steps are as follows:
[0044] 1) Weigh 16 parts of polyvinyl chloride resin, 12 parts of calcium carbonate and 27 parts of bamboo wood by weight;
[0045] 2) Add calcium carbonate to a ball mill for ball mill dispersion treatment for 1 hour, and filter through a 10-mesh sieve to obtain calcium carbonate powder;
[0046] 3) The bamboo wood is cut into 3mm chopped fibers by a chopping machine, and filtered through a 10-mesh screen; bamboo wood powder is obtained;
[0047] 4) Add polyvinyl chloride resin, calcium carbonate powder and bamboo wood powder to a 110r / min mixer and knead for 32 minutes to obtain a mixed material. The working temperature of the mixer is 180°C;
[0048] 5) Transfer the mixed material obtained in step 4) to a twin-screw extruder with a host speed of 23r / pm for shearing and extrusion, and after water cooling and molding of the sizing die, the door panel base material is formed;
[0...
PUM
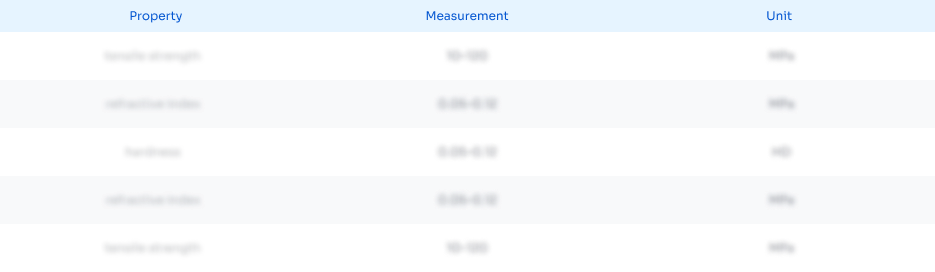
Abstract
Description
Claims
Application Information

- R&D
- Intellectual Property
- Life Sciences
- Materials
- Tech Scout
- Unparalleled Data Quality
- Higher Quality Content
- 60% Fewer Hallucinations
Browse by: Latest US Patents, China's latest patents, Technical Efficacy Thesaurus, Application Domain, Technology Topic, Popular Technical Reports.
© 2025 PatSnap. All rights reserved.Legal|Privacy policy|Modern Slavery Act Transparency Statement|Sitemap|About US| Contact US: help@patsnap.com