Direct-current motor speed-position double-closed-loop anti-interference PID control method and system
A DC motor and control method technology, applied in electric controllers, controllers with specific characteristics, etc., can solve the problems of complex design methods and difficult applications of high-order controllers and nonlinear controllers, and achieve convenient and extensive design. Application, the effect of improving control accuracy
- Summary
- Abstract
- Description
- Claims
- Application Information
AI Technical Summary
Problems solved by technology
Method used
Image
Examples
Embodiment 1
[0050] figure 1 It is a flowchart of Embodiment 1 of the speed-position double-closed-loop anti-disturbance PID control method for a DC motor of the present invention. see figure 1 , the DC motor speed-position double closed-loop anti-disturbance PID control method includes:
[0051] Step 101: Obtain a set desired angle position value.
[0052] Step 102: Filtering the set desired angular position value to obtain a filtered set desired angular position value.
[0053] This step 102 specifically includes:
[0054] according to Calculate the filtered set desired angular position value in, f y (s) is the filter, ω f is the filter bandwidth, s is the complex frequency domain variable commonly used in control theory, y * (s) is to set the desired angular position value.
[0055] Step 103: Obtain the actual measured angle position value.
[0056] Step 104: Comparing the filtered set desired angular position value with the actual measured angular position value to obtain...
Embodiment 2
[0068] figure 2 It is a schematic diagram of the control process of the speed-position double-closed-loop control in Embodiment 2 of the speed-position double-closed-loop anti-disturbance PID control method for a DC motor of the present invention. see figure 2 , in the DC motor speed-position double closed-loop anti-disturbance PID control method, the control process of the speed-position double closed-loop control specifically includes:
[0069] Set desired angular position y * (s), after filter F y After (s), it is compared with the actual measured position y(s) to form a position tracking error e y (s), through the anti-disturbance PD controller C PD After (s), get the expected speed value u y (s), compared with the actual measured speed n(s), forming a speed tracking error e n (s), through the anti-disturbance PI controller C PI After (s), the control quantity u is formed n (s) (voltage amount), and finally form the speed regulation and position regulation of the...
Embodiment 3
[0096] Figure 6 It is a structural diagram of Embodiment 3 of the DC motor speed-position double closed-loop anti-disturbance PID control system of the present invention. see Figure 6 , the DC motor speed-position double closed-loop anti-disturbance PID control system includes a filter 601 , a first comparator 602 , a position loop anti-disturbance PD controller 603 , a second comparator 604 and a speed loop anti-disturbance PI controller 605 .
[0097] The filter 601 is used to filter the input desired set angle position value, and output the filtered set expected angle position value.
[0098] The filter 601 specifically includes:
[0099] filtering unit for the Calculate the filtered set desired angular position value in, f y (s) is the filter, ω f is the filter bandwidth, s is the complex frequency domain variable commonly used in control theory, y * (s) is to set the desired angular position value.
[0100] The first comparator 602 is connected to the filter...
PUM
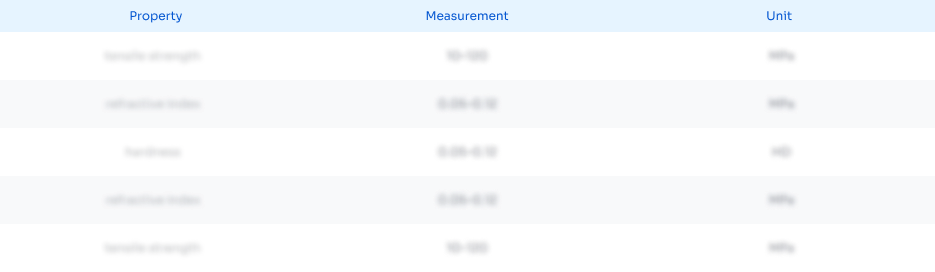
Abstract
Description
Claims
Application Information

- R&D Engineer
- R&D Manager
- IP Professional
- Industry Leading Data Capabilities
- Powerful AI technology
- Patent DNA Extraction
Browse by: Latest US Patents, China's latest patents, Technical Efficacy Thesaurus, Application Domain, Technology Topic, Popular Technical Reports.
© 2024 PatSnap. All rights reserved.Legal|Privacy policy|Modern Slavery Act Transparency Statement|Sitemap|About US| Contact US: help@patsnap.com