Method for preparing battery-grade lithium carbonate from lithium sulfate crude ores and recovering byproducts
A technology of lithium carbonate and lithium sulfate, applied in lithium carbonate;/acid carbonate, alkali metal sulfite/sulfite, chemical instruments and methods, etc. Incomplete recovery, large seasonal dependence and other problems, to achieve the effect of reducing the amount of impurities generated, reducing losses, and low cost consumption
- Summary
- Abstract
- Description
- Claims
- Application Information
AI Technical Summary
Problems solved by technology
Method used
Image
Examples
Embodiment 1
[0047] In this example, coarse lithium sulfate ore from a certain sulfate-type salt lake brine in Tibet is used, and the content of lithium sulfate is 17.25%.
[0048] The technological process of this embodiment is as Figure 1~3 As shown, it includes the process of preparing battery-grade lithium carbonate, recovering by-products gypsum, bischofite, borate mixed salt and Glauber's salt, and recycling part of the solution in the process.
[0049] 1. First, the process of preparing battery-grade carbonic acid is as follows: figure 1 Shown: Specifically include the following steps:
[0050] 1. Primary washing: crush and grind lithium sulfate coarse ore to obtain particles with a particle size of less than 2mm, send them into the washing reactor, and use pulp washing liquid to wash lithium sulfate coarse ore at 65°C; Before the filtrate L5, the washing liquid adopts lithium chloride mother liquor L1 (concentration is 350g / L) and sodium sulfate solution L2 (concentration is 350...
PUM
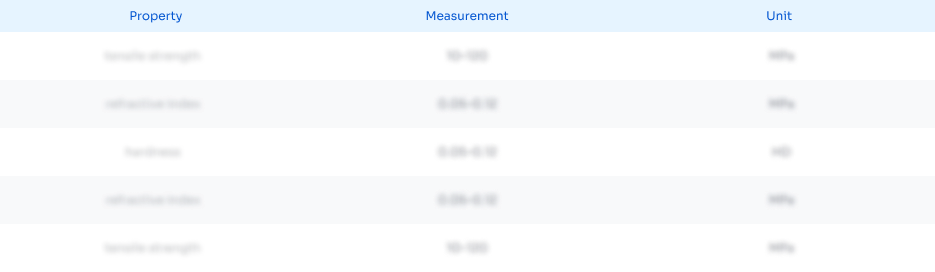
Abstract
Description
Claims
Application Information

- Generate Ideas
- Intellectual Property
- Life Sciences
- Materials
- Tech Scout
- Unparalleled Data Quality
- Higher Quality Content
- 60% Fewer Hallucinations
Browse by: Latest US Patents, China's latest patents, Technical Efficacy Thesaurus, Application Domain, Technology Topic, Popular Technical Reports.
© 2025 PatSnap. All rights reserved.Legal|Privacy policy|Modern Slavery Act Transparency Statement|Sitemap|About US| Contact US: help@patsnap.com