A process for producing nodular cast iron camshafts by clamping sand molds with iron molds
A ductile iron and camshaft technology, applied in the core, mold, mold composition and other directions, can solve the problems of low strength and elongation, unqualified metallographic structure, and high production cost, and achieve high strength and elongation. The metallographic structure is qualified and the cooling effect will not be too fast
- Summary
- Abstract
- Description
- Claims
- Application Information
AI Technical Summary
Problems solved by technology
Method used
Image
Examples
Embodiment Construction
[0035] The process of producing a nodular cast iron camshaft by clamping sand molds with iron molds of the present invention will be further described in detail below in conjunction with the accompanying drawings.
[0036] The process of producing nodular cast iron camshafts by clamping sand molds with iron molds of the present invention uses gray cast iron to pour special iron molds to make special casting frames, places the special iron molds on the special casting frames, and uses double-sided horizontal sand injection molding machines to produce coatings Sand mold, place ceramic filter and glass fiber filter in the sand mold, bond the left and right sand molds to form a complete sand mold, place the sand molds one by one in the middle of the iron mold, and make the sand mold accurately embedded in the cavity of the iron mold. The molten iron after chemical treatment is poured into sand molds one by one, and the castings are separated. The specific production process include...
PUM
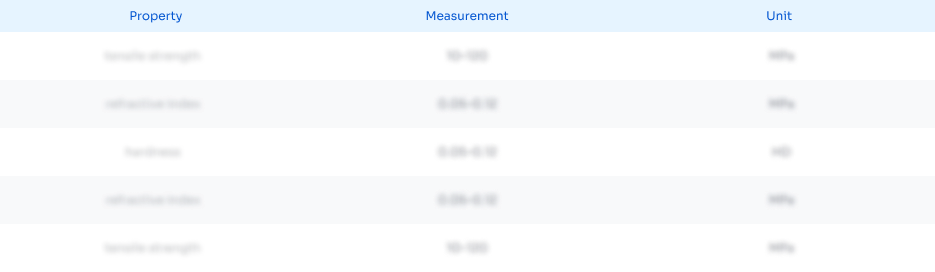
Abstract
Description
Claims
Application Information

- R&D
- Intellectual Property
- Life Sciences
- Materials
- Tech Scout
- Unparalleled Data Quality
- Higher Quality Content
- 60% Fewer Hallucinations
Browse by: Latest US Patents, China's latest patents, Technical Efficacy Thesaurus, Application Domain, Technology Topic, Popular Technical Reports.
© 2025 PatSnap. All rights reserved.Legal|Privacy policy|Modern Slavery Act Transparency Statement|Sitemap|About US| Contact US: help@patsnap.com