Automatic control system for girder erection
An automatic control system and beam erection technology, applied in general control systems, control/adjustment systems, program control, etc., can solve the problems of low erection efficiency, error-prone, safety accidents, etc., so as to improve installation efficiency and reduce the possibility of , Improve the effect of safety protection
- Summary
- Abstract
- Description
- Claims
- Application Information
AI Technical Summary
Problems solved by technology
Method used
Image
Examples
Embodiment 1
[0047] The invention provides an automatic control system for erecting beams, including:
[0048] The RTK receiver 21 is located beside the winch of the crane of the beam erecting equipment, and is used to locate the spatial coordinates of the crane;
[0049] The hoisting height encoder 22 is arranged on the main shaft of the hoist of the crane of the beam erecting equipment, and is used for positioning the spatial coordinates of the spreader;
[0050] The main girder control station is located in the operating room of the girder erection equipment, and communicates with the RTK receiver 21 and the hoisting height encoder 22; Coordinates; it is also used to automatically generate beam erection schemes and send beam erection instructions according to the spatial coordinates of the crane, the spatial coordinates of the spreader and the boundary conditions of the beam erection control;
[0051] The crane control station is located on the traversing trolley of the crane of the gi...
Embodiment 2
[0081] In the process of lifting the beam, safety protection is particularly important. In order to solve the problem of safety protection in the construction process, further optimization is carried out on the basis of Embodiment 1, and relevant measures for safety protection are implemented by using safety protection devices. In this embodiment, the safety protection device includes an inclination sensor 24, an anti-collision indicating device 25, a load sensor 26, and an RFID positioning device. Such as figure 2 As shown, the details are as follows:
[0082] The portable inclination sensor 24 is placed on the prefabricated beam 31 , and the specific position is not limited. In this embodiment, it is described as an example, and placed on the upper surface of the prefabricated beam 31 by adsorption. The detection signal of the inclination sensor 24 is sent to the control system through its own wireless transmission module. When it is detected that the change in the longi...
PUM
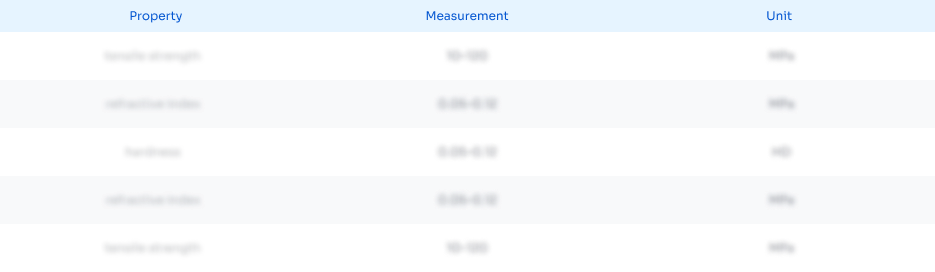
Abstract
Description
Claims
Application Information

- Generate Ideas
- Intellectual Property
- Life Sciences
- Materials
- Tech Scout
- Unparalleled Data Quality
- Higher Quality Content
- 60% Fewer Hallucinations
Browse by: Latest US Patents, China's latest patents, Technical Efficacy Thesaurus, Application Domain, Technology Topic, Popular Technical Reports.
© 2025 PatSnap. All rights reserved.Legal|Privacy policy|Modern Slavery Act Transparency Statement|Sitemap|About US| Contact US: help@patsnap.com