Urea injection system controlled by common rail-type valve group and control method thereof
A urea injection system and valve group control technology, which is applied in the electronic control of exhaust gas treatment devices, diagnostic devices of exhaust gas treatment devices, and exhaust gas treatment, etc. problems, to achieve the effect of saving costs and ensuring injection accuracy
- Summary
- Abstract
- Description
- Claims
- Application Information
AI Technical Summary
Problems solved by technology
Method used
Image
Examples
Embodiment Construction
[0049] The following specific examples illustrate the present invention in further detail.
[0050] Such as Figure 1-2 As shown, a urea injection system controlled by a common rail valve group provided by the present invention includes: a urea tank 1, a plurality of urea nozzles 2, a cooling water pipeline 3, a compressed air pipeline 4, a urea pipeline 5, and an air release pipeline 6 , a plurality of purge pipelines 7 , and a valve group injection unit 8 .
[0051] The connection relationship between each pipeline is: the cooling water pipeline 3 flows through the urea tank 1, the compressed air pipeline 4 includes a total air pipeline 43 drawn from the air source, and the total air pipeline 43 is divided into a parallel first air pipeline 41 and a parallel one. Multiple second air pipelines 42, the first air pipeline 41 leads to the urea tank 1, each second air pipeline 42 leads to each urea nozzle 2, and the urea pipeline 5 includes the total urea pipeline 51 drawn from ...
PUM
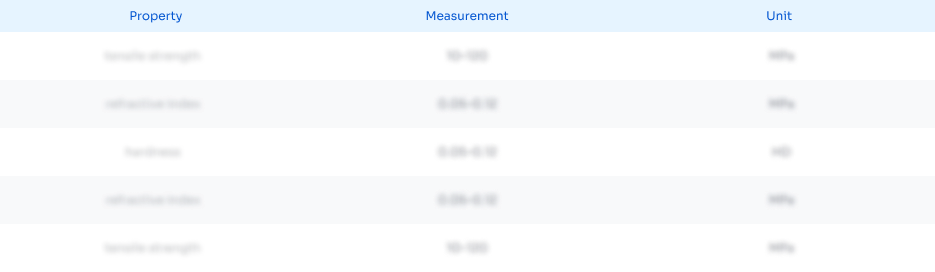
Abstract
Description
Claims
Application Information

- R&D
- Intellectual Property
- Life Sciences
- Materials
- Tech Scout
- Unparalleled Data Quality
- Higher Quality Content
- 60% Fewer Hallucinations
Browse by: Latest US Patents, China's latest patents, Technical Efficacy Thesaurus, Application Domain, Technology Topic, Popular Technical Reports.
© 2025 PatSnap. All rights reserved.Legal|Privacy policy|Modern Slavery Act Transparency Statement|Sitemap|About US| Contact US: help@patsnap.com