Electroplating process
A technology of electroplating process and electroplating device, which is applied in the direction of electrolysis process and electrolysis components, etc., can solve the problems of low electroplating efficiency of hollow column parts, achieve good effect and facilitate washing
- Summary
- Abstract
- Description
- Claims
- Application Information
AI Technical Summary
Problems solved by technology
Method used
Image
Examples
specific Embodiment approach 1
[0036] As shown in the figure, an electroplating process includes the following steps:
[0037] Step 1: placing the tube to be electroplated in the electroplating device for rinsing;
[0038] Step 2: acid-activating the tube;
[0039] Step 3: washing the tube;
[0040] Step 4: Copper-plating the tube;
[0041] The above-mentioned electroplating process also includes an electroplating device, which includes a flat plate 1, an extension rod 101, a ring body 102, a wheel notch 103, a shaft I 104 and a wheel 105, and the left and right sides of the lower end of the flat plate 1 are fixedly connected with an extension Rod 101, the lower ends of two extension rods 101 are all affixed with a ring body 102, and the front and rear sides of each ring body 102 lower side are all provided with a wheel notch 103, all affixed on each ring body 102 Two shafts I 104 and four shafts I 104 are respectively located in the four wheel notches 103 , and each shaft I 104 is rotatably connected to...
specific Embodiment approach 2
[0043] As shown in the figure, the electroplating device also includes an intermediate connecting seat 2, a combined base 5 and a motor IV501, the intermediate connecting base 2 is fixedly connected to the middle part of the upper end of the plate 1, and the lower side of the right end of the combined base 5 is fixedly connected to the motor IV501, and the motor IV501 The output shaft passes through from the back to the front and is rotatably connected to the combination seat 5, and the upper side of the intermediate seat 2 is fixedly connected to the output shaft of the motor IV 501. Start the motor Ⅳ501, the output shaft of the motor Ⅳ501 drives the middle connecting seat 2 to rotate, and the middle connecting seat 2 drives the plate 1 to rotate around the axis of the output shaft of the motor Ⅳ501. , which in turn changes the part from landscape orientation to portrait orientation.
specific Embodiment approach 3
[0045]As shown in the figure, the electroplating device also includes an electric push rod III6, a support plate 601, a board seat 602, an electric push rod IV603, a supporting plate 604, and a turntable 605. The electric push rod III6 is fixed to the support plate 601, and the support plate 601 is fixed Connected to the upper end of the plate 1, the board base 602 is fixed to the movable end of the electric push rod III6, the lower end of the board base 602 is fixed to the electric push rod IV 603, and the movable end of the electric push rod IV 603 is fixed to the supporting plate 604, and the supporting plate 604 Turn the connection dial 605 . Start the electric push rod Ⅲ6, the electric push rod Ⅲ6 is used to move the turntable 605 left and right, start the electric push rod Ⅳ603, and the electric push rod Ⅳ603 is used to move the turntable 605 up and down, so that the turntable 605 is adjusted to the right side of the part, so that the part After the right end is attached...
PUM
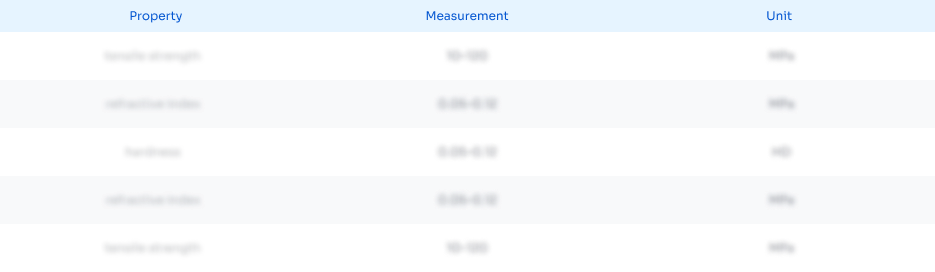
Abstract
Description
Claims
Application Information

- Generate Ideas
- Intellectual Property
- Life Sciences
- Materials
- Tech Scout
- Unparalleled Data Quality
- Higher Quality Content
- 60% Fewer Hallucinations
Browse by: Latest US Patents, China's latest patents, Technical Efficacy Thesaurus, Application Domain, Technology Topic, Popular Technical Reports.
© 2025 PatSnap. All rights reserved.Legal|Privacy policy|Modern Slavery Act Transparency Statement|Sitemap|About US| Contact US: help@patsnap.com